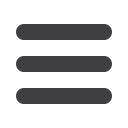

Technology News
www.read-tpt.com68
N
ovember
2012
Industrial Ethernet in geometric
control of cast iron pipes
IN order to check the ovality and the
flange geometry of cast iron pipes, MEL
has implemented a system solution with
M2-iLAN laser scanners. The system is
able to achieve an accuracy of 0.1mm.
The flexible Ethernet cable, moved by
the robotic arm, has a great influence on
achieving this precision.
The manufacturing of steel pipes is
usually subject to a thermal process.
Duktus manufactures pipes complete
with flange and connection profile using
centrifugal casting. Upon the cooling
of a pipe, different material distortion
often develops, giving the pipe an oval
shape. So that the pipe meets the
high quality requirements, it must be
measured accurately after cooling and,
if necessary, be mechanically reworked.
In addition to ovality, the flange and the
connection profile are also checked at
the pipe ends for errors and chips.
Until now, the measurement has been
made with a manually operated contact
measuring system at individual points.
The subsequent bending process has
been manually initiated and controlled.
Duktus now uses a system based on
two MEL Mikroelektronik GmbH M2-
iLAN scanners. The system solution
has been integrated into the automated
manufacturing process and controls the
entire measuring and bending process
fully automatically with its own logic. The
operator’s long-standing experience,
along with its empirical findings, is
incorporated.
The pipes to be measured are moved
by a PLC-controlled transport system
into the holding device of the hydraulic
bending press, which serves as a
measuring station. The measuring device
consists of a linear table with precision
drive, which adjusts the spacing of the
two scanners, depending on the pipe
diameter to be measured. The linear
table itself is attached to a robotic arm
and is guided by the latter into the pipe
end to be measured. The pipe diameter
is determined prior to the insertion of
the measuring device in the pipe with
an M10L laser sensor, allowing the pipe
inner diameter and the geometric centre
of the pipe to be determined.
During the measuring procedure,
the linear table is rotated 180°. Both
scanners detect, during a measuring
period of about two seconds, the ovality
of the pipe as well as the geometry of the
circumferential connection profile. The
data collected by the scanners is sent in
real time via Ethernet to the evaluation
PC. The MEL software calculates the
deviations from the nominal dimension
and also the resultant bending
parameters.
The software then controls the
rotation of the pipe into the correct
bending position. The bending machine
is addressed with the necessary
parameters, and the bending process
follows. After bending, a control
measurement is made in order to record
the success of the bend.
Different pipe diameters as well as
differences in the flange and connection
profiles require a flexible measuring
system to be used. The system
solution used is able to detect pipes
with diameters ranging from 350 to
1,100mm. Different flange profiles can
be stored in the software. The operator
can therefore customise the system to
changes in the production line. The MEL
software arranges and coordinates the
individual components involved in the
process with one another. Initiated by
the material control, which moves the
pipe to be measured into the holding
device of the bending machine, the MEL
software controls the entire measuring
and bending process. This is possible
since the acquisition of the measured
values and their evaluation both take
place within the software.
MEL Mikroelektronik GmbH
–
Germany
Email:
b.rohloff@melsensor.deWebsite:
www.melsensor.deMEL M2-iLAN laser scanners