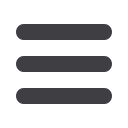

WCN
Issue N° 43
www.iwma.org30
The presence of mischmetal was
justified as being required to
promote fluidity, wettability and
absence of intergranular corrosion.
Cerium and lanthanum are
expensive rare earth metals,
increasing the cost of coating.
From a financial point of view, their
presence is undesirable, but are
they required to give the technical
improvements they are credited
with?
Regarding high temperature perfor-
mance, no differences were seen
with regards to the wires coated
with (3.4mm 1083) and without
(1.85 1005) mischmetal additions.
A study done at Bekaert
(8)
has
shown that 35-50% of mischmetal
in the hot dip alloy bath is lost as
dross.
The mischmetal present in the
coating can be up to 10x less than
that in the molten bath (
Figure 21
).
The greater the mischmetal addi-
tion, the greater the amount of
dross produced.
When more than 0.02% mischmetal
is present, processing is seriously
hindered.
With regards to corrosion, relatively
little effect is seen on performance
in the humidity chamber (
Figure 22
).
Electrochemical potential tests in
both 5% aqueous NaCl (
Figure 23
)
and 0.05 M K2SO4 (
Figure 24
) show
no significant effect of mischmetal
additions on corrosion rate.
Conclusions
Information from trials concerning
the high temperature behaviour of
hot-dip zinc and zinc aluminium
coatings has been presented.
For 3.4mm high carbon (0.83% C)
ACSR zinc and zinc-5% aluminium
coated core wires, no problems
other than a small loss in salt spray
resistance have been found at
temperatures at 190°C for up to
185 days.
However, a low carbon zinc coated
wire was found to show increased
alloy layer growth and wrap test
problems after 120 days at 190°C.
Actual % Ce+La in Coating
Actual % Ce+La in Melt
Accelerated Humidity Test – Bezinal Samples 150g/m
2
Corrosion Rate (µm loss per year)
Concentration Al ( %)
Corrosion Rate as a fuction of % Ce, % La in % Al in
0.05 M K
2
SO
4
% Ce+La in Coating
Minimum hours to failure
Measured values
240/gm
2
Measured values
150/gm
2
Figure 21
▲
▲
:
Mischmetal contents in melt and coating
(8)
Figure 22
▼
▼
:
Effect of mischmetal additions on humidity test
(8)
Figure 23
▼
▼
:
Effect of mischmetal additions on corrosion rate in electrochemical potential test in 5% aqueous NaCl
(8)
100% WR
% Ce
% La
% Al
Linear (% Al)
Linear (% Ce)
Linear (% La)
Concentration Ce & La (both in %)