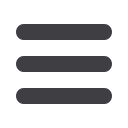

WCN
Issue N° 43
www.iwma.org26
The average operating temperature
for such a cable is typically around
80°C. However, due to increasing
trade in the power market, the need
for conductor capacity has increased
while moratoriums have limited the
construction of new lines for environ-
mental and economic reasons.
This has now resulted in the need for
power lines to be capable of higher
capacities. With this comes the need
for the lines to be able to withstand
higher temperatures.
When this is combined with peak
periods of usage, the cable operating
temperature could rise as high as
250°C. This can be of concern for
traditional zinc hot-dip coatings due to
their temperature sensitivity.
Galvanised coatings are sensitive to
temperature due to iron-zinc diffusion
phenomena across the steel/coating
interface which lead to the creation
of a number of iron-zinc intermetallic
compounds (some of which can be
brittle) at the coating-steel interface
referred to as the alloy layer (
Figure 2
).
This alloy layer is initially formed during
the galvanising temperature, but its
growth stops as it is cooled. However,
with sufficient subsequent reheating it
is possible for the alloy layer to grow
again. Because the diffusion of iron
and zinc atoms do not occur at the
same speed, it is possible to create
voids (the Kirkendall effect) between
the unalloyed top layer of zinc and alloy
layer, making the free (unalloyed) zinc
layer susceptible to peeling (
Figure 3
).
Different values have been given for
the maximum safe use temperature of
galvanised coatings.
Steel manufacturers advised 245°C
in the early 70s
(2)
, but more recently
the American Galvanizer’s Association
stated that galvanised coatings have
an extended time upper service
temperature of around 200°C
(1)
.
Zn-Al coatings, such as Bezinal and
Galfan, offer an alternative to standard
zinc galvanising coatings. Wire Zn-Al
coatings are usually based near the
zinc-aluminium eutectic composition,
near 5% aluminium.
In the case of Galfan, small mischmetal
additions between 0.03 and 0.1%
(mainly of lanthanum and cerium) are
also specified
(3, 4)
. However, the value
of these additions is in question and is
discussed later in this article.
Zinc-5% aluminium coatings are well
known for their significantly better
corrosion performance in comparison
to standard zinc (about 3x better salt
spray resistance)
(5, 6)
.
In addition, the microstructure of such
coatings is quite different to that of
hot dip zinc, especially with regards
to the nature of the alloy layer and the
absence of the brittle Fe-Zn binary
compounds mentioned above.
Thus, one would also expect
differences in response of the coating
to temperature.
This paper compares the response of
Zn and Zn-Al coated wires in terms
of microstructure, wrapping properties
and corrosion to different exposure
times at various elevated temperatures
with and without mischmetal additions.
In addition to coating, the influence of
steel type is also examined.
Finally, some observation the influence
of mischmetal additions to Zn-5%Al
coatings are made.
In this paper, the designation Zn5Al
refers to a coating composition close to
that of the Zn-5% Al eutectic, but may
be found to vary slightly from close to
the eutectic composition to slightly
above in terms of aluminium content.
Experimental Exposure of
Zn and ZnAl Coated Wires
to Elevated Temperatures
Actual 1/0 AWG 6X1 Raven ACSR
cables containing both Zn5Al (with
Figure 2
▲
▲
:
Iron-zinc compounds (with associated hardnesses) at the coating/steel interface
Figure 3
▲
▲
:
Peel-off of free zinc layer due to the
formation of voids (the Kirkendall effect) resulting
from zinc-iron diffusion at elevated temperatures
(1)
Figure 4
▲
▲
:
Arrangement of ACSR segments in oven
Figure 5
▼
▼
:
Microstructures of 3.4mm ACSR 1083
core wires from start to 185 days at 190°C (note:
variation in total coating thickness is normal for
hot-dipped coatings)
Figure 6
▼
▼
:
Microstructures of 1.85mm core 1005
wires from start to 185 days at 190°C. Start
microstructures are from 150g/m
2
. Note only
alloy layer is present in the case of the Zn coating
exposed for 185 days (free zinc has peeled off)