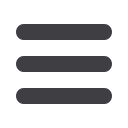

WCN
Issue N° 43
www.iwma.org31
As temperature increased, faster
alloy layer growth, and consequently
wrapping test failures after shorter
exposure times were observed to
occur for both steel types having zinc
coatings, but not zinc-5% aluminium
coatings.
Zinc-5% aluminium coatings have
shown temperature resistance for
periods at above 300°.
Exact resistance times for zinc coated
wires at elevated temperatures
may likely be dependent on wire
composition.
At temperatures over 200°C, corrosion
resistance of zinc-5% aluminium
coated wires may actually improve
slightly.
Cerium and lanthanum mischmetal,
required for the Galfan
®
specification,
do not have a significant impact in a
well regulated Zn5Al coating operation.
As much as half of such additions to
the hot dip bath are wasted in the form
of dross.
The mischmetal that does remain in
the coating was observed not to have
significant impact on many aspects of
corrosion resistance.
This paper was given at the Istanbul
Cable & Wire ‘09 conference,
2
nd
November 2009. The authors
were presented with the Harry W
Bennett Ferrous speaker award at wire
Düsseldorf 2010.
References
(1)
“High Temperature Applications,” Dear Dr Galv,
American Galvanizer, Vol 47, 2000
(2)
H W Adams, “Steel Supported Aluminum
Conductors (SSAC) for Overhead Trans-
mission Lines,” Paper T 74 054-3, IEEE PES
Winter Meeting, 1973
(3)
S F Radtke, D Coutsouradis and J Pelerin,
US Patent 4448748, “Zinc-Aluminum Alloys
and Coatings,” 1984
(4)
ASTM A856: “Specification for Zinc-5%
Aluminum-Mischmetal Alloy-Coated Carbon
Sheet,” American Society for Testing and
Materials
(5)
H Dewilde, “Galfan: A Breakthrough in the
Corrosion Protection of Wire Products,”
International Technical Conference on
Wire Technology, S
ã
o Paulo, Brazil, 1996,
pp 97-105
(6)
“Zinc-aluminum coating: management of
Galfan
®
lines,” R Branders and A Stacey,
Wire Journal International, Nov 2008
(7)
K Manchiraju, “Examination of Galvanized VS
Bezinal Coated Steel Samples,” MP2003020,
Southwire, 2004
(8)
C Blakeman, G Lagae, J Karasek, Bekaert
Internal Report, 2003
Figure 24
▲
▲
:
Effect of mischmetal additions on corrosion rate in electrochemical potential test in 0.05M aqueous
K2SO4
(8)
Corrosion Rate as a fuction of % Ce, % La in % Al in
5% NaCI
Corrosion Rate (µm loss per year)
Concentration Ce & La (both in %)
Concentration Al ( %)
% Ce
% La
% Al
Linear (% Al)
Linear (% Ce)
Linear (% La)
Charles Coffin,
Hans Depamelaere, Dale King
and Walther Van Raemdonck,
NV Bekaert SA,
Belgium
Email:
info@bekaert.comWebsite:
www.bekaert.com