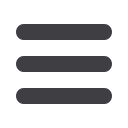

WCN
Issue N° 43
www.iwma.org27
exemplified for the 3.4mm 1083 wires
in
Figures 8
-
9
). A summary of the
alloy layer growth at 190°C is shown
in
Figure 10
for the 3.4mm 1083 and
1.85mm 1005 wires.
Figure 11
shows
the impact of temperature on the
3.4mm 1083 wires.
The results of the trials can be
summarised as follows:
Growth of the alloy layer in the
1
Zn5Al coated wires could not be
observed under any of the trial
conditions, only globularising of the
aluminium-rich phase
No growth of the alloy layer in the
2
Zn coated 3.4mm 1083 ACSR
core wires is observed at the
190°C trials; however growth of
the alloy layer of the 1.85mm 1005
Zn coated wire was noticed after
120 and 185 days
Growth of the alloy layer on the
3
3.4mm Zn coated 1083 ACSR
core wire is first observed at
225°C, two weeks as was also
seen with coatings on the 1.85mm
wires. All higher temperatures
also saw similar growth at this
time or less. Growth of the alloy
layer in the Zn5Al coated 3.4mm
1083 ACSR core wire could not
be observed under any of the trial
conditions, only globularising of the
aluminium-rich phase
The greater sensitivity of the 1.85mm
1005 wire to temperature with respect
to alloy layer growth is most likely to be
mischmetal) and Zn hot dip coating
on 3.4mm 1083 core wires (having
a carbon content of about 0.83%)
were heated in an oven (
Figure 4
) on
perforated stainless steel shelves
with a fan-driven room atmosphere
ventilation.
Additional 1.85mm AISI 1005 wires
coated with similar 270gm
2
coating
weights of Zn and Zn5Al (without
mischmetal) were also tested at the
same time to reveal differences in
34 coating behaviour. Cable/wire
lengths were about 20cm.
Both ends of the ACSR cables were
fixed with pipe clamps to avoid
unravelling.
Trials were done at the following
conditions:
190° C – 15,30, 62, 121 and 185
•
days (ACSR 3.4mm 1083 and
1.85mm 1005)
225°C – 14 and 28 days (3.4mm
•
1083 without Al conductors and
1.85mm 1005)
245°C – 14 days (ACSR and
•
3.4mm 1083 core wires without Al
conductors, 1.85mm 1005) and 35
days (ACSR cables and 1.85)
300°C – 1 day (3.4mm 1083 wires
•
with and without Al conductors,
1.85mm 1005)
Microstructures
Figures 5
and
6
show microstructures
of the ACSR core-wires in the ‘before
test’ condition and after 185 days
(end of test) at 190°C for the 3.4mm
1083 and 1.85mm 1005 wire coatings,
respectively.
For the 3.4mm wires at 190°C, no
significant difference in alloy layer
growth can be observed for neither
galvanised nor Zn5Al coatings.
However, for the 1.85mm 1005 steel,
changes in the galvanised coating alloy
layer could be could be measured, at 121
and, especially at 185 days (
Figure 7
).
At all temperatures over 200°C, alloy
growth was seen in the Zn coatings,
but none in the Zn5Al coatings (as
Time (Days)
Alloy Layer (µm)
Time (Days)
Alloy Layer (µm)
Figure 7
▲
▲
:
Microstructures of 1.85mm Zn-coated
wires showing growth in alloy coating at various
times up to 185 days at 190°C. Note vacancy
formation between alloy layer and zinc top layer.
The voids near the surface could also be related to
this phenomenon as they were not observed on
Zn5Al coated wires
Figure 8
▲
▲
:
Microstructures of 3.4mm ACSR core
wires after 14 and 28 days at 225°C
Figure 9
▲
▲
:
3.4mm ACSR core wire microstructures
after 245°C, 35 days
Figure 10
▼
▼
:
Plot of alloy thickness against time for wires studied
Figure 11
▼
▼
:
Plot of alloy thickness as a function of time and temperature for the 3.4mm 1083 wires
225°C
14
days
28
days
121
days
185
days
190ºC
62 days
245°C, 35 days