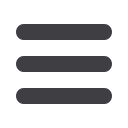

WCN
Issue N° 43
www.iwma.org24
Precision Rolling acquired
by ASMAG UK
Precision Rolling has been acquired by ASMAG UK
Ltd. Precision Rolling specialises in equipment for the
manufacture of simple and complex profiles in low to
high-carbon steels and non-ferrous materials.
David Liddle, managing director of ASMAG UK Ltd,
commented: “We are delighted to extend our product range
through this acquisition. Precision Rolling offers an extensive
range of profile manufacturing equipment, together with
ancillary machinery, that enables complete production lines
to be designed, built and installed.”
Mr Liddle continued: “Following the takeover of a German
supplier some years ago, and now the recent acquisition,
ASMAG can offer a complete and comprehensive solution
to the wire industry.”
ASMAG UK Ltd is the UK division of ASMAG –
Anlagenplanung und Sondermaschinenbau GmbH, a
leading Austrian supplier of copper, brass, steel, stainless
steel and aluminium tube manufacturing equipment.
ASMAG UK’s full range of products, ancillaries and services
includes:
Single stand units
•
Multi-stand lines
•
Powered and non-powered edge rolling
•
Turks heads
•
Friction turks heads with single or double capstans
•
Single or double pass machines
•
Horizontal or vertical drawing drums
•
Ancillary equipment
•
Payoffs and spoolers
•
ASMAG UK Ltd – UK
:
info@asmaguk.comWebsite
:
www.asmaguk.comMarldon was founded in 1966 by
Ernie Hindle and John Buckley (later a
chairman of the IWMA), both of whom
had “grown up” in the wire and cable
industry.
Over
succeeding
decades
the
company developed a wealth of
experience and, importantly, a portfolio
of equipment that spans a wide range
of handling processes in wire and
cable production. For this reason the
company now frequently hears from
its customers, “Oh, I didn’t realise you
did…I only know you for airwipes/
traverses/flyers/chalkers etc.”
To address this issue, Marldon
has adopted a pictorial approach
to highlighting its capabilities by
publicising a graphic (shown above)
that gives interested parties a feeling
for the areas in which Marldon
operates. More detail is available on
the company’s website.
Marldon Group Ltd – UK
Fax
: +44 870 907 0016
:
sales@marldon.comWebsite
:
www.marldon.comMarldon’s new explanatory graphic
▲
▲
What exactly does Marldon do?
Filtration of high viscosity
lubricants
Filtration systems are designed to keep operating fluid as
clean as possible by removing particles loosened during the
drawing operation. Pure filtration of coolants and lubricants
will give higher productivity, due to fewer wire breaks,
reduced down time, less wear of the dies and improved
surface quality of the wire. To achieve these goals, RESY
developed and introduced the Compact-Band-Filter (KBF),
now in use for over 30 years.
For high viscosity lubricants (over 120 cSt) which are
mostly used for aluminium, band filters are not suitable.
In these cases, the separation of the particles occurs
by sedimentation in the system tank. This has to be cleaned
on a regular basis. The sludge collected at the bottom is
discharged, together with a big proportion of the lubricant.
Another effect of fine aluminium flitters (flakes) is that the
viscosity of the medium increases. This higher concentration
affects the whole supply and cooling system.
At wire Düsseldorf 2010, RESY presented its new filtration
and delivery system, especially developed for this
application. The unit consists of a centrifuge, a delivery
pump, a heater, cooling system and electrical control. It is
of modular construction to be adaptable to the customer’s
need, and can be easily integrated in existing systems.
Lubricant is cleaned and cooled continuously during
operation. The concentration of the particles in the lubricant
stays at an acceptable level and ensures high quality of the
wire and a consistent drawing process. Maintenance efforts
and discharge costs will be reduced by this new system and
higher productivity achieved.
Reber Systematic GmbH & Co KG – Germany
Fax
: +49 7121 948338
:
info@resy-filtration.comWebsite
:
www.resy-filtration.com