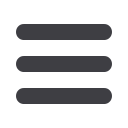

J
uly
2008
www.read-tpt.com116
›
New strategies for wall thickness measurement
in the hot seamless tube production plant
Holger Gurski-Schramm, Ingenieurbüro Gurski-Schramm & Partner, Germany
and Dr Marc Choquet, Tecnar Automation Ltee, Canada
1. Introduction
The competitive nature of the current world economy has
placed new emphasis on productivity, quality control and energy
consumption of production facilities. Market demands have placed
added pressure on manufacturers to better control production and
minimize fabrication and rejection of out-of-specifications products.
In particular, the tube steel industry has felt such market pressure.
Production efficiency of high quality product such as mechanical
tubing has been constantly increasing in the past few years. Low
volume productions per batch have also increased the demands on
production teams to rapidly achieve final specifications of products
with low numbers of ‘test’ units.
Sensors have been an integral part of this process. Sensors
placed on the production line allow the plant operator to control
the production parameters as well as quickly react to unexpected
situations. A large part of the increase in productivity is the result of
an extensive use of sensors.
Mechanical tubes are used in applications such as hydraulic
cylinders and power transmission components (gears and bearing),
which place strict controls on mechanical dimension. Wall thickness
sensors have been used routinely to control the production of
mechanical tube. Until recently, however, the availability for online
wall thickness sensors has been limited.
Penetrating radiation (
γ
-rays) techniques have been developed and
used for thickness gauging of tubes. However, such techniques
have limitations on the location where they can be installed.
Penetrating radiation gauges cannot measure wall thickness with
a mandrel inside or adapt easily to rapid side-motion of the tube.
In addition, there is a limit to the range of wall thickness and outer
diameter sizes that a penetration radiation system can measure.
Laser-ultrasonics, which combines the precision of ultrasonics with
the flexibility of optical systems, has provided an advanced method
to measure online wall thickness under plant conditions
[1]
. With
laser-ultrasonics, the presence of a mandrel does not affect the
wall thickness measurement. In addition, since the laser-generated
probing pulse is always launched in a direction normal to the
surface, large tube motion cannot be tolerated without affecting the
accuracy of the wall thickness measurement.
Finally, the size of the outer diameter of a tube does not impose any
limitations on the ability to measure. The flexibility of laser-ultrasonic
allows for wall thickness measurement at the output of processing
tools. It therefore permits ‘real-time’ data for automated feedback
control on location, which was not possible in the past.
2. Online ultrasonic wall thickness
measurement with ultrasonics
Standard ultrasonics inspection is a renowned non-destructive
technique that provides several parameters of interest for materials
and process control. Ultrasonic wall thickness gauges are used in
several industries, such as aircraft inspection and metallic thickness
gauging, because it provides high accuracy measurements. Minute
changes in wall thickness are easily detected and quantitatively
measured.
Conventional ultrasonics (UT) utilise a piezoelectric transducer
(PZT) to generate and detect the sound waves used to probe the
material. A PZT, stimulated with an appropriate electrical signal, will
impact the outer surface of the tube to which it is attached.
The resulting pulse (ultrasonic pulse) will then travel to the inner
wall of the tube, where it will be reflected back towards the outer
surface. The reflected signal is called the echo. Measurement of the
travel time of the probing pulse directly provides the thickness of the
tube, based on the velocity of sound in the alloy of the tube (which
is a physical property of the alloy).
Conventional UT requires a good mechanical contact between
the PZT and the inspected tube to be able to have a measurable
signal. Such a method is therefore difficult and often impossible to
use when the tube is at high temperature or moving rapidly, such as
encountered in a steel mill production line. Commercial UT systems
are available for ‘offline’ tube dimensioning, but require a wait-period
for product cooling, which may take several hours. Non-contact
ultrasonic sensors are needed for inspection of high-temperature
moving materials.
Conventional UT also requires a strict orientation of the PZT with
respect to the surface of the material, in order to get a strong signal
into the bulk of the material and achieve true wall thickness. This
involves measurement of the travel-time solely in the direction
normal to the surface. Angular tolerance for proper operation is
only about a few degrees. Any deviation from the angular tolerance
results in a rapid decrease of signal amplitude. Strict angular
Figure 1
:
Typical on-line laser-ultrasonic signal from hot tube (WT=15mm)