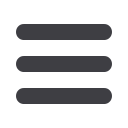

117
J
uly
2008
www.read-tpt.com›
orientation with conventional ultrasonics is very difficult to sustain
on moving or bouncing materials, such as tubes under production
line conditions.
3. Online ultrasonic wall thickness
measurement with laser-ultrasonics
The above limitations are eliminated by laser-ultrasonics. In laser-
ultrasonics, laser light is used for generation and detection, at a
distance, of the ultrasonic pulse. Since no mechanical contact is
made between the sensor and the tube, the temperature of the
tube does not affect the performance of the sensor. Furthermore,
in laser-ultrasonics the source of ultrasonic generation is located
directly on the surface of the tube. The detection of ultrasounds is
made by monitoring the motion of the same surface at the same
location.
In effect, the surface of the tube becomes the sensor in laser-
ultrasonics. It can be shown that the orientation of the laser light
with respect to the normal direction to the surface of the material
does not affect the generation and detection of the ultrasonic signal.
Hence, no particular orientation between the laser-ultrasonic sensor
and the surface of the inspected material is needed. This allows
laser-ultrasonic inspection to be insensitive to the bouncing of the
tube.
Laser-ultrasonics is a combination of two separate laser methods:
laser generation of ultrasounds and laser detection of ultrasounds.
Laser generation of ultrasounds is a technique that has been in
use since the early development of pulsed lasers
[2]
. Efficient laser
generation of ultrasounds on metal is performed by applying a
strong laser pulse onto the surface of the material, which causes
ablation or vaporization of a small quantity of the material at the
point of impact of the laser. Following the ablation, a recoil force is
produced, which is the source of a compression ultrasonic pulse.
The compression pulse is always launched in a direction normal to
the free surface of the tube (ie the surface of impact of the laser
beam) independently of the angle of incidence of the laser light.
Hence, travel-time of the ultrasonic pulse is always recorded in the
direction normal to the surface, giving the correct wall thickness.
It should be recognised that for high temperature steel, the blown-
off material of the ablation is the oxide covering the surface. The
oxide is rapidly regenerated at these elevated temperatures and
therefore no visible mark is seen once the material is cooled to an
ambient temperature.
Laser detection of ultrasound is based on frequency-demodulation
by an optical interferometer of the laser light reflected or
backscattered from the surface of the material
[3]
. A laser light is
focused on (or near) the point of impact of the generation laser
beam on the surface of the material. Any surface motion at the point
of impact of the detection laser is recorded in the reflected light
as an optical frequency variation (slight change of ‘colour’). The
ultrasonic surface displacement is therefore ‘encoded’ in the laser
light, called the signal beam.
After ‘extraction’ from the signal beam, the resulting information
is identical to a conventional ultrasonics waveform, often called
A-scan in non-destructive inspection, as shown in figure 1. The
signal contains a strong initial pulse, called the ‘surface signal’,
corresponding to the initial impact of the generation laser beam on
the surface of the tube, followed by several pulses, which are the
echoes resulting from the forward propagation and reflection from
the back wall of the initial ultrasonic pulse.
The travel-time of the ultrasonic pulse within the bulk of the tube
is obtained by measuring the time between the initial surface
impact and the time of arrival of the first echo. Numerical
signal enhancement methods are used to get a high accuracy
measurement of the travel-time. The values recorded are then
scaled with the appropriate velocity of sound for the material of the
tube and corrected for thermal expansion.
It should be recognised that since velocity of sound in a material
is a function of temperature, the temperature of the tube must
also be recorded simultaneously with the measurement of the
laser-ultrasonic signal. The LUT gauge makes this simultaneous
measurement using an optical pyrometer. The temperature is
measured at the same location as the laser-ultrasonic signal. The
scaling value, used to convert travel-time to thickness, is adjusted
using the temperature measurement and the steel alloy category of
the produced tube.
The heart of a laser-ultrasonic system is the optical interferometer.
Several optical interferometers are available, each with their own
advantages and limitations. Tecnar Automation Ltee (Tecnar)
is a world leader in the development and manufacture of laser-
ultrasonics equipment, including laser-ultrasonic demodulators.
Following developments made at Tecnar, an active interferometer
approach has been developed, based on two-wave beam mixing
[4]
,
specifically for online wall thickness measurement of hot tubes in
the harsh operation of steel mill.
By taking wall thickness measurement as function of the length of
the tube, wall thickness length-profiles are obtained, as shown in
the figure below. The ‘signature’ of the wall thickness length-profile
is identical to the length-profile obtained with a conventional UT
system for tube, with the exception that the data shown in the figure
was obtained online and displayed in real-time.
The shape of the length-profile is used by operators to identify
the source of ‘out of specifications’ production and appropriate
correction measures can be taken. The length-profile shown in
figure 2 is typical of a tube with large eccentricity. The rapid variation
(cycle) of the wall thickness comes for the detection of minimum
and maximum wall thicknesses of the tube as it is rotated before the
LUT probe.
4. The LUT (laser ultrasonic thickness) gauge
The LUT gauge is the latest implementation of laser-ultrasonic
technology for online wall thickness measurement of hot tube.
The LUT includes the most advanced laser-ultrasonic technology
Figure 2
:
On-line wall thickness measurement using LUT gauge