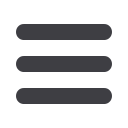

119
J
uly
2008
www.read-tpt.com›
The choice of the support structure is dependant on the data needed
and the location on the plant floor where the LUT is used. Figure 3
shows the probe mounted on a rapid swivelling device. This unit
is used when circumference information is required at a location
where the tube is not rotating (from the production process).
5. Implementation of LUT gauges
The flexibility of the LUT allows it to be installed at locations not
possible with other measuring technology. The first implementation
of the LUT was installed directly at the output of a rotary sizer. In
this location the main feature regarding the selection of LUT was
the capability of the LUT to record data in the presence of large
lateral motions (bouncing) of the tube.
Being at the end of the manufacturing process (immediately before
the cooling bed), the length-profile signatures allowed the operator
to detect problems anywhere ‘upstream’ in the production line. LUT
data enabled detection of problems such as splitting of the piercing
mandrel and velocity imbalance of the rollers of the stretch-reducing
mill. As of August 2004, this first implementation of the LUT has
already inspected over 2,000,000 tubes.
As an example of the use of the LUT, figure 5 shows a set of online
tube length-profiles. The first length-profile (top) shows a case
of bulging of the wall thickness in the centre section of the tube.
The second (bottom) length-profile shows the tube produced once
remedial action had been taken. Without the LUT, the conventional
method of cutting the tube endings and manually measuring them
would not have detected the extent of the defect in produced tube.
A second location where the LUT has been installed is at the output
of a free floating mandrel mill. In this instance, the important feature
for selection of the LUT was the capability of the LUT to record
data if the presence of a mandrel. As it is near the beginning of the
manufacturing process, the length-profile data allowed the operator
to detect problems at the piercing but also gave some information
for correction of the specifications using the next processing steps.
This configuration is currently in use in Japan.
As described earlier, the LUT measures the wall thickness at a
known distance from the start (top) of the tube. This distance is given
by the length-measuring device included in the LUT. This ‘point’
measurement allows the operator to determine where, within the
length of the tube, the problem has occurred. This can be indicative
of the source of the problem. In addition, the ‘point’ information can
be use to locate specific features of the tube. For example, the LUT
can provide the length of the plug for a plug mill and provide the
possibility of feedback control for cutting of the plug.
6. Conclusion
Laser-ultrasonic technology is the most advanced technology for
the online wall thickness measurement of hot tubes. With the LUT,
the Laser Ultrasonic Thickness gauge manufactured by Tecnar
Automation Ltee, the technology is commercially available for use
in harsh environments and has been used on a tube production
plant since 2002.
The LUT now allows for possible measurements of real wall
thickness during a production flow at different locations, which were
not available with previous technologies. Eccentricities of different
orders and wall thickness fluctuations over the full length of the
tube can be detected with the intention to readjust the process, to
produce tubes with better quality and to save material. Thus, the
measurement results allow for fast reaction on the process to avoid
out of tolerance production.
References
Monchalin J-P,
1.
‘Progress towards the application of laser-ultrasonics in industry’
,
Review of Progress in Quantitative Nondestructive Evaluation, vol 12, Edited
by D O Thompson and D E Chimenti (Plenum Publishing Corporation, 1993),
pp 495-506.
C B Scruby and L E Drain,
2.
‘Laser-Ultrasonics: Techniques and Applications’
(Adam Hilger, Bristol, UK,1990)
J-P Monchalin,
3.
‘Optical detection of ultrasound’
, IEEE Trans Sonics, Ultrasonics,
Freq Control, UFFC-33, pp 485-499 (1986).
A Blouin and J P Monchalin,
4.
‘Detection of ultrasonic motion of a scattering
surface by two-wave-mixing in a photorefractive GaAs crystal’
, Applied Physics
Letters, 65, 932-934, (1994).
This article was presented at the International Tube Association’s
Tube Ukrainian conference in Dnepropetrovsk, Ukraine in 2007.
Ingenieurbüro Gurski-Schramm & Partner
– Germany
Fax
: +49 203 37809 26
:
info@gurski.bizWebsite
:
www.gurski.bizTecnar Automation
– Canada
Fax
: +1 450 461 0808
:
mchoquet@tecnar.comWebsite
:
www.tecnar.com
Figure 5
:
Set of wall thickness measurement with LUT for production
correction