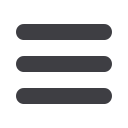

EuroWire – July 2008
61
technical article
This means the stress in the primary coating
at room temperature is a hydrostatic tensile
stress. It increases as temperature decreases
further until reaching the primary coating T
g
(typically ~-20ºC), when the primary coating
also turns into the glassy state. The calculated
tensile stress in the primary coating is ~0.8
MPa at room temperature as shown in
Figure 2
. Due to the visco-elastic property of
the secondary coating, the actual stress level
should be lower than the calculated stress
and decrease with time as the secondary
coating undergoes stress relaxation at sub-T
g
temperatures.
[5]
While the risk of coating cavitation by
thermal stress is low for typical dual-coated
fibres, precautions must be taken to evaluate
certain types of coating systems discussed
below. The new developmental trend
for primary coatings is to further reduce
their modulus and T
g
to provide improved
micro-bending buffering protection over
a wide temperature range. In this type of
coating system, the tensile stress keeps
building up as temperature begins to drop,
yet the primary coating remains in its rubbery
state. As shown in
Figure 3
, the calculated
tensile stress increases linearly with tem-
perature decrease. The stress relaxation of
the secondary coating is also much slower at
low temperatures. In addition to the risk of
high thermal stress, a lower modulus primary
coating may also be more prone to cavitation,
due to its lower crosslink density.
It is therefore very important that primary
coatings with low modulus and low T
g
be
carefully designed to have high cavitation
strength through optimum structure of the
crosslinking network.
In-depth knowledge of the cavitation
resistance of UV curable coating materials at
the molecular level allows the development
of coating systems having improved micro-
bending performance combined with high
cavitation strength, to assure robust fibre
performance over a wide temperature range.
Another example of a high-risk situation with
regard to cavity formation is fibre with thicker
than standard coating layers.
The tensile stress in the primary layer of a
fibre with the glass/coating OD structure
of 125/350/500 μm is calculated and also
plotted in
Figure 3
. The tensile stress in the
primary coating of this fibre is 2.8 times the
stress level of that in the primary coating of a
standard 245 μm OD coated fibre. Therefore,
fibres having thicker coating layers should
be composed of a primary coating having
high cavitation strength in combination
with a secondary coating having faster stress
relaxation.
2.1.2 Cavity formation in the primary coating.
Figure 4
shows microscope images of some
cavities formed in a 500 μm OD coated
fibre, after temperature cycling between
85ºC and -60ºC. Irregularly shaped coating
ruptures of different sizes can be observed
in the primary coating layer. The fact that
the coating ruptures are wide open, shown
as voids, indicates the presence of a tri-axial
tensile stress in the primary layer at room
temperature.
From fracture mechanics theory, the
parameter representing the cavitation
resistance of a material is called cavitation
strength. When the tri-axial stress reaches
this critical point, the material starts to
rupture and form internal cavities. It has
been calculated and proved experimentally
that for an ideal rubber, the tri-axial stress
for a very small spherical hole to be inflated
unboundedly is (5/6)E, where E represents
the Young’s modulus.
[6]
Any microscopic
network defect in the material may serve as
the initial rupture site.
This means for a 1 MPa primary coating,
a tri-axial tensile stress of 0.83 MPa can
already cause cavity formation according to
the un-bounded growth mechanism, if the
coating material behaves like an ideal rubber.
By proper molecular design of the coating’s
cross-linked network structure, the desired
high cavitation resistance can be achieved,
with the cavitation strength significantly
exceeding the coating modulus.
In this type of high cavitation strength
primary coatings, small cavities will not grow
un-boundedly and the material will not
rupture even under a relatively high tensile
stress level that could be present in the
primary coating.
2.2 Cavities induced by the mechanical
stress
In addition to the hydrostatic thermal tensile
stress, cavity formation in primary coatings
can also be driven by anisotropic tri-axial
stress resulting from a mechanical impact
on the coated fibre. It has been previously
reported that coating tears were observed
under high tension, when pulling fibre
through a re-winder assembly to test the
coating’s resistance to de-lamination.
[4]
When an external mechanical force is exerted
on a coated fibre, the coating layers will
de-form and result in a non-uniform stress
field in the coating material.
Figure 5
schematically illustrates the defor-
mation of the coating layers under a lateral
force F. Since the secondary coating is a
much harder material than the primary
coating, the secondary layer behaves like a
hollow tube being pressed under the lateral
pressure with the shape of the tube changing
to oval, but with no deformation on coating
thickness. The primary coating is bonded
on both sides with glass and secondary and
is forced to deform internally. The areas of
primary coating along the force direction
are compressed and the areas perpendicular
Figure 3
▼
▼
:
Calculated thermal stress vs temperature for a regular 250µm fibre (assuming the stress starts to develop
below secondary Tg ~50°C)
Figure 4
▲
▲
:
Cavities in the primary coating layer
induced by temperature cycling in a 500µm fibre
(left) 40x (right) 200x
Figure 5
▲
▲
:
A schematic diagram of the localised
tensile stresses in the primary coating by a
mechanical lateral force
Figure 6
▲
▲
:
Mean normal stress in the primary
coating layer induced by a mechanical lateral force
calculated by Finite Element Analysis