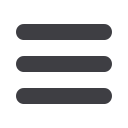

EuroWire – Juillet 2008
82
article technique
valeur de la contrainte dans le revêtement
primaire d’une fibre revêtue standard d’un
diamètre extérieur de 245 μm. Il s’ensuit
que les fibres présentant des couches de
revêtement plus épaisses devraient être
composées par un revêtement primaire à
haute résistance à la cavitation associé avec
un revêtement secondaire à relaxation en
contrainte plus rapide.
2.1.2 Formation de cavités dans le revêtement
primaire.
La
Figure 4
montre des images au
microscope de certaines cavités s’étant
formées dans une fibre revêtue avec un
diamètre extérieur de 500 μm, après une
variation cyclique de la température entre
85ºC et -60ºC. Des ruptures du revêtement
de forme irrégulière et de dimensions
différentes peuvent être observées dans
la couche du revêtement primaire. La
présence de ruptures bien ouvertes
dans le revêtement, représentées sous la
forme de vides, indique l’existence d’une
contrainte triaxiale dans la couche primaire
à température ambiante.
Pour la théorie mécanique de la fracture,
le paramètre représentant la résistance à la
formation de cavités dans un matériau est
défini résistance à la cavitation. Lorsqu’une
contrainte triaxiale atteint ce point critique,
le matériau commence à se déchirer et à
former des cavités internes.
Il a été calculé et prouvé expéri-
mentalement que dans le cas d’un
caoutchouc idéal, la contrainte triaxiale
pour élargir un trou sphérique de petites
dimensions est égale à (5/6)E, où E
représente le module de Young.
[6]
Tout
défaut de réticulation microscopique
dans le matériau peut constituer le point
de rupture initial. Cela signifie que, pour
un revêtement primaire de 1MPa, une
contrainte de traction triaxiale de 0,83MPa
peut déjà causer la formation de cavités
selon un mécanisme d’accroissement
illimité, dans le cas où le matériau de
revêtement se conduirait comme un
caoutchouc idéal. Avec une conception
moléculaire appropriée de la structure
réticulée du revêtement, l’on peut
obtenir la résistance élevée à la cavitation
désirée, avec des valeurs de résistance à la
cavitation considérablement supérieures
au module du revêtement.
Dans ce type de revêtement primaire à
haute résistance à la cavitation, les cavités
de petites dimensions ne s’accroîtront pas
sans limites et le matériau ne subira aucune
rupture même dans le cas de valeurs de
contrainte de traction relativement élevées
dans le revêtement primaire.
2.2 Cavités induites par contraintes
mécaniques
Outre la contrainte hydrostatique et
thermique, la formation de cavités dans
les revêtements primaires peut être
également causée par des contraintes
triaxiales anisotropes résultant d’un
impact mécanique sur la fibre revêtue.
Durant quelques essais de résistance
du revêtement au délaminage, réalisés
en tirant la fibre à travers un système de
rembobinage, il a été remarqué que le
revêtement se déchire lorsque soumis à
des tensions élevées.
[4]
Lorsqu’une force mécanique extérieure est
appliquée à une fibre revêtue, les couches
de revêtement se déforment en générant
un champ de contraintes non uniforme
dans le matériau de revêtement. La
Figure
5
illustre schématiquement la déformation
des couches de revêtement soumises
à une force latérale F. Le revêtement
secondaire étant un matériau beaucoup
plus rigide que le revêtement primaire, la
couche secondaire se conduit comme un
tuyau vide, soumis à une pression latérale,
passant de la forme tubulaire à une
forme ovale, mais sans entraîner aucune
déformation de l’épaisseur du revêtement.
Le revêtement primaire est collé des
deux côtés au verre et au revêtement
secondaire, et il doit se déformer par force
à l’intérieur. Les zones du revêtement
primaire en direction de la force sont
comprimées, et les zones perpendiculaires
à la direction de la force sont soumises à
un allongement. La contrainte de traction
dans ces zones soumises à un allongement
présente un composant triaxial significatif
pouvant causer la cavitation du revêtement
primaire au cas où la contrainte dépasserait
la résistance à la cavitation du revêtement.
La
Figure 6
représente un champ de
contrainte normal moyen calculé par
l’Analyse des Éléments Finis dans la
couche du revêtement primaire d’une
fibre avec une géométrie d’un diamètre
extérieur de 125/240/410 μm, soumise
à une contrainte latérale simulée. Le
résultat montre quantitativement les
différents champs de contrainte allant
de la contrainte de compression (-) à
la contrainte de traction (+). Comme
illustré par la
Figure 6
, les zones soumises
à la contrainte de traction majeure sont
constituées par les points perpendiculaires
à la direction de la force appliquée et
à proximité de l’un et l’autre côté des
interfaces entre le verre et le revêtement
primaire, et entre le revêtement primaire
et le revêtement secondaire. Ce sont les
zones où la cavitation est particulièrement
susceptible de se manifester lorsqu’une
force mécanique latérale est appliquée.
La
Figure 7
illustre quelques exemples de
cavités induites intentionnellement dans
le revêtement primaire, causées par des
impacts mécaniques latéraux. La force
latérale doit être dynamique avec la vitesse,
soit longitudinalement (glissement), soit
perpendiculairement (frappe). Une force
latérale statique ne peut avoir pour résul-
tat que le délaminage. Dans la
Figure 7
,
l’impact mécanique a été créé en faisant
glisser une barre métallique d’un diamètre
de 1mm longitudinalement par rapport à
la fibre.
Avec un appareil réalisé en attachant la
barre métallique à un dispositif d’essai
de frottement automatique, des vitesses
contrôlées et des forces contrôlées ont
été appliquées en ajoutant des poids
différents à l’appareil. Tant la vitesse que
la force d’impact influencent la contrainte
induite dans le revêtement. À des vitesses
très basses, le délaminage a lieu plutôt que
la cavitation du revêtement.
Figure 7
▼
▼
:
Exemples de formation de cavités/délaminage dans la couche du revêtement primaire causés par impacts
mécaniques latéraux
Figure 8
▼
▼
:
Préparation de l’échantillon pour l’essai de résistance à la cavitation
Plaque de verre
Résine (100 μm )
Barre de quartz