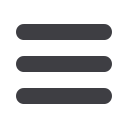

EuroWire – November 2007
73
newmachinery & equipment
launched in 2007
New soldering experience
Cooper Hand Tools has created a new soldering experience with the WR3M Weller,
a winner of the red dot design award for 2007.
This versatile repair station is tailored to the needs and requirements of professional
repairs to latest-technology electronic sub-assemblies in industrial production
engineering. Three independent tool channels with automatic tool detection
guarantees the simultaneous operation of three soldering tools.
Precise temperature control performance at the soldering tip is guaranteed by the
digital control electro-technology, together with superior-quality sensor and heat-
transfer technology. High-speed measured-value acquisition provides for maximum
temperature precision and optimum dynamic temperature performance in load
situations. All high-speed micro tools from Weller can be connected, while the new
Weller hot air pencil HAP 200 offers increased power.
Further advantages for the user are the USB port and the vacuum channel for pick-
up. Innovative special functions such as automatic channel changing, temperature
pre-selection buttons for each channel and factory calibration check guarantee high
operation simplicity. The big LCD display allows clear information and simple handling.
Cooper Tools GmbH – Germany
Fax
: +49 7143 580 108
:
marketing-europe@cooperhandtools.deWebsite
:
www.cooperhandtools.com/europeWR3MWeller – winner of the red dot design award for 2007
▲
Bacchetti sas, Italy, specialises in the design and manufacture of motor-driven de-
coilers, both for coils and reels, designed for the wire and cable industry for the feeding
of spring making machines, straightening machines and cable cutting machines. The
de-coiler HSB 200 has been designed for reels (with maximum diameter 760mm
and width 315mm) and for the feeding of high performance wire and cable cutting
machines. The de-coiler is designed to allow an easy positioning of the reel between
the cones using traditional lifting devices.
The material to de-coil goes from the reel to a first diversion device, and then to a
pulley. The rotation of the motor is controlled by this loop-control device. All the
operating parameters of the de-coiler can be set on the control panel. The maximum
speed is 90rpm and the capacity is 200kg. Also in production the de-coiler HSB 80 will
provide a maximum capacity of 80kg.
This new product widens the range of de-coilers with horizontal axis of rotation
produced by the company.
Bacchetti sas – Italy
Fax
: +39 04977 3997
:
m.bacchetti@tin.itWebsite
:
www.bacchetti-amb.comMotor-driven de-coiler HSB 200