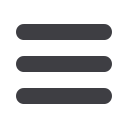

EuroWire – November 2007
77
english
The electrical current flow is ensured by
using appropriate clamps at the entries
and a solid aluminium cup.
Short-circuit tests as well as permanent
current tests have proven the capability
and reliability of the design.
2.3.4 Weather station
In order to complete the monitoring
system and to get the relevant
environmental data, a small weather
station was added. It is independent
of a power supply, energised by a solar
panel.
Figure 7
shows the weather station
mounted on the tower top.
The data, air temperature, humidity,
wind speed and direction is transferred
to the control computer via a wireless
connection.
2.3.5 Data processing and control unit
In order to use the FBG sensors for a
monitoring system controlled by an
ordinary PC, their wavelength coded
optical signals have to be converted into
a data stream. Two steps are necessary:
first an optical to electrical conversion and
finally an A/D conversion. The outgoing
data is transferred to a PC via a serial
RS232 interface.
The whole µ-processor controlled unit fits
into a 19" rack for indoor use or can be
delivered in a robust case for outdoor use.
Figure 8
presents a partial view of the
processing unit with four optical fibre
cables on the left hand side, carrying
the data from the FBG temperature
and strain sensors and the outgoing
RS232 data.
The monitoring software runs on any
PC and can be adopted to the actual
situation or needs.
With the data from the weather station
sent to the computer, the power line
operator gets a comprehensive set of
information to manage his lines.
3. Field installation
After a simulation of the temperature and
strain monitoring system in 2005 which
proved the feasibility of the idea, a field
installation was performed in April, 2006.
The long time between the feasibility
study and the field installation was due
to the fact of looking for a power line
with an already installed OPPC where a
Distributed Temperature System (DTS)
based on Raman scattering could be
implemented.
After finding an appropriate line and a co-
operating power utility, the data of the line
and the accompanying conditions were:
• A 110 kV line equipped with a 243-
AL1/39-ST1A phase conductor
• Connecting
optical
underground
cable to be blown into a duct between
the installation tower and substation
building; its length: 1,000m
• Installation time for the connecting
cable and system: 2 days, with a 4 hour
outage time for the line
In order to fulfill the electrical requirements
for the separator, a 123 kV, pollution class
IV, T-branch type with a total height of
1.83m and a weight of 33kg was selected.
Normally, a separator used on an OPPC
line is completely installed on site. But
because of the tough time schedule
and the sensible work of inserting the
FBG sensors into the jumper cables,
the jumpers including the separator
fixing clamps were already assembled in
the plant.
The underground cable blowing was
arranged for the first day; that left the
second day for the rest of the installation:
• final assembly of the separator
including all splice works and its fixing
on the tower
Figure 5
:
FBG strain sensor attached to clevis strap
▲
Figure 6
:
T-branch separator
▲
Figure 7
:
Autonomous, wireless weather station
▼
Figure 8
:
Signal processing unit
▼
Figure 9
:
Completely assembled separator prior
to lifting
▼
Figure 10
:
Separator top – details of cable entries
▼