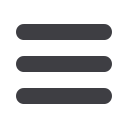

EuroWire – November 2007
75
english
Power Line Monitoring
System for Force and
Temperature
By Reinhard Girbig and Norbert Fink, Draka Comteq Germany GmbH & Co KG, Mönchengladbach, Germany
1. Introduction
The deregulation of energy markets with
its increasing numbers of wind parks
and small power plants is forcing power
utilities to look for new strategies in
planning and operation of overhead lines.
One of the strategies is the optimisation
of power transmission on the existing
infrastructure. For such considerations
the main parameters are the temperature
of the conductor and the mechanical
stress of the wire. They determine the
existing reserves in transmission capacity
limited by the maximum allowed tem-
perature of the metals and the critical sag
and ground clearance.
Until now, operation of overhead
lines required safety margins for the
temperature which is usually evaluated
through almost obsolete calculation pro-
cedures and assumptions.
An economical use of the reserves of
an existing line is hardly possible. The
presented fibre based overhead line
monitoring system allows for on-line
and remote measurement of the inner
temperature and the mechanical stress of
a conductor.
The use of such a system generates a
return of investment in very short time on
highly loaded lines inside a power grid.
High mechanical stress due to ice can also
be detected and preventive measures can
be taken before the towers collapse.
In addition, it can verify the planning
data and assumptions for the construction
of grid extensions.
2. System Description
2.1 General Overview
Existing temperature and force monitoring
techniques for phase conductors are based
either on mechanical or on optical fibre
systems. The former have limited lifetime
and reliability and are less accurate than
optical fibre systems. Fibre systems, so far,
use Raman scattering where the ratio of
intensity of the Stokes and anti-Stokes line
of the scattered spectrum is proportional
to the temperature.
For such a system
[1]
, usually a phase
conductor has to be replaced by a
complete OPPC (Optical Phase Conductor)
cable length making the system expensive.
To avoid the installation of a new cable,
the presented system uses the correlation
between the conductor temperature and
temperature of the jumper cable bridging
two sections of a line at a tension tower.
Instead of replacing a whole cable length,
only a short jumper cable housing a sensor
fibre is used.
Contrary to the Raman-based fibre system,
the sensor is realised as a Fibre Bragg
Grating (FBG) using the thermo-optic
effect to measure temperature.
One end of the jumper cable is entering
a separator where the sensor fibre is
spliced to an ordinary fibre leading down
the tower for further data transmission;
the other end is connected to the phase
conductor as usual.
Figure 1
shows the
principle of the temperature monitoring
system.
By adding strain sensors, also using FBG
technology, and a small weather station
mounted on the tower, a complete power
line monitoring system has been realised.
The signals from the FBG sensors can be
either processed in a small unit mounted
to the tower or transported to another
location by an optical underground cable
or an existing OPGW link.
In both cases, one processing unit can
handle signals from several locations.
2.2 Fibre Bragg Grating – Principle
Fibre Bragg Gratings are made by creating
a periodic variation in the refractive
index of an optical fibre. This can be
realised by irradiation of the fibre with
intense UV laser light
[2,3]
.
Figure 1
:
Temperature monitoring – Principle
set-up
▲
Figure 2
:
Fibre Bragg Grating - Principle
▲