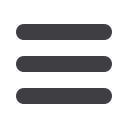

50
Wire & Cable ASIA – May/June 2016
www.read-wca.comFeature
Furnaces & heat treatments
QED specialises in equipment for in-line heat-treating, cleaning and coating of steel wire. Its furnaces are custom-built for
multi-strand annealing, stress relieving, patenting and tempering processes.
With a bed of fine aluminium oxide particles and precise air and gas control, its fluidbed furnaces offer an environmentally
friendly heat-treating solution in an energy efficient package. The fluidbed’s rapid heat transfer results in significantly shorter
furnace length and therefore more compact and easier to operate process lines. These fluidbeds operate from DV=120 to
DV=240 and from 1.5 t/h to 8 t/h production with satisfied customers on six continents.
A powerful S7 Siemens PLC is at the heart of QED’s furnace
control systems. Programmed with user-friendly software and
advanced combustion algorithms, they deliver precision gas
flow and accurate temperature control. One of the interesting
new developments is a web-enabled system for smartphone
monitoring and remote troubleshooting of control panels.
The addition of pulse firing technology to QED’s muffle tube
austenitising furnace improves the thermal efficiency and
increases temperature uniformity. This is due to the higher than
average flame velocity and superior convective heat-transfer.
Pulse firing also offers lower NOx emissions and more flexibility
in burner and zone control.
With a view to improved efficiency and to minimise
environmental impact, QED developed the dual loop pressure/
temperature combustion control system. This patented system
maintains a steady output with precise air-gas ratio on all
multiple burner furnaces.
The latest development in ceramic lined furnaces is the
advanced recuperative technology Mark 4 immersion burner,
which offers dramatically higher combustion efficiency from
an extended double pass pre-heat design. Constructed of
stainless and high nickel alloy steels, this new burner offers
an extended operating lifespan, a cooler skin temperature and
reduced maintenance.
QED – Canada
Website
:
www.qedwire.comNo. 871 is a 2,000°F (~1,093.3°C) gas-heated box furnace from
Grieve, currently used for heat treating and high temperature
testing.
650,000 BTU/HR are installed in three modulating natural gas
burners with a floor mounted combustion air blower. Workspace
dimensions are 30" wide x 48" deep x 30" high.
The unit has 7" insulated walls comprised of 5" of 2,300°F
ceramic fibre and 2" of 1,700°F block insulation. The 6½" floor
insulation is made of 4½" of 2,300°F firebrick and 2" of 1,900°F
block insulation. The plate hearth is made of firebrick and is
supported by firebrick piers.
Controls onboard No. 871 include a Partlow MRC 7000 recording
and programming temperature controller and an electrically
operated vertical lift door.
Grieve Corporation – USA
Website
:
www.grievecorp.com❍
The No. 871
gas-heated box
furnace from Grieve
Experience and innovation
Heat treating and high temperature
testing
❍
Two of QED’s galvanising lines at Mid-South in Nashville, USA