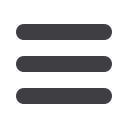

53
www.read-wca.comWire & Cable ASIA – May/June 2016
24" wire specimens affixed with Kraft paper strips at their
tops were suspended vertically in a draft-free chamber.
A 37 ±1 MJ/m
3
methane flame was impinged upon the
samples at an angle of 20° to the vertical.
The impingement point of the flame was 254 ±2mm below
the bottom of the Kraft paper strip. A continuous layer of
surgical cotton was placed below the specimens such
that the surface of the cotton was 235 ±6mm below the
impingement point of the flame.
Each specimen was subjugated to five 15-second appli-
cations of flame. The interval between flame applications
was 15 seconds and the interval was maintained for all
applications where the specimen self-extinguished prior to
the elapse of the 15 seconds.
For samples burning longer than 15 seconds but shorter
than 60 seconds, the next application of flame was done
when the sample self extinguished. In order for a sample to
have passed the VW-1 burn test, all of the following criteria
must have been met:
• Less than 25 per cent of the Kraft paper indicator was
burned
• The specimen did not burn longer than 60 seconds
after any of the five applications of flame
• The cotton batting was not ignited by either flaming or
glowing particles or flaming drops
In addition to these criteria, the burn performances of
the specimens in this study were characterised by the
following parameters:
• Uncharred length – the distance below the Kraft paper
indicator that is not burned and maintained a smooth,
unblemished surface after wiping with a soft cloth
• Average burn time – the duration that the specimen
continued to burn after the removal of the flame and
averaged over the five flame applications. For burn
durations greater than 60 seconds, the time was
measured until the Kraft paper began to burn
3 Results and Discussion
3.1 Effect of insulation thickness
The effect of insulation thickness on the performance of
multiple compositions in a VW-1 type test is shown in
Figure
1
for 14 AWG solid Cu conductors. The results show that
for the two higher flame-retardant compositions, the burn
duration decreases as insulation thickness increases with
❍
❍
Figure 2
:
Effect of insulation thickness on uncharred length in
VW-1 type test for different FR formulations (solid conductors)
30 mil
60 mil
Uncharred length (mm)
❍
❍
Figure 3
:
Effect of conductor type on burn duration for different
formulations for 30 mil insulation thickness
❍
❍
Figure 4
:
Effect of conductor type on burn duration for different
formulations for 60 mil insulation thickness
no burn time recorded for the 60 mil insulation with VB-1
formulation. These results are in line with the expectation
that for insulation or articles made with flame-retardant
materials, it is increasingly difficult to start a sustainable
fire.
The data also shows that for the less flame-retardant
material, ie, for HB-1 sample in this case, the opposite may
be true.
This observation can be easily explained by the fact that
below a minimum level of flame-retardance when thicker
materials do catch and support a sustaining flame, they
will just burn longer because of the larger mass of available
flammable material. For both cases with HB-1 formulation,
the wire samples burn all the way through the flag leaving
no uncharred length.
The effect of insulation thickness on the burn behaviour
can also be expressed by the uncharred length of the
samples as shown in
Figure 2
.
The results are shown only for the VW-1 rated samples
as the horizontal burn rated sample burns through the
entire length of the wire leaving no uncharred length. It is
seen that for both the formulations, the uncharred length
is higher for the thicker sample, indicating a greater
flame-retardance with increase in thickness.
The data also suggests that VB-1 is better than VB-2 in
flame-retardance as evidenced by the higher uncharred
length and shorter burn duration.
Solid
Stranded
Burn duration (sec)
Solid
Stranded
Burn duration (sec)