
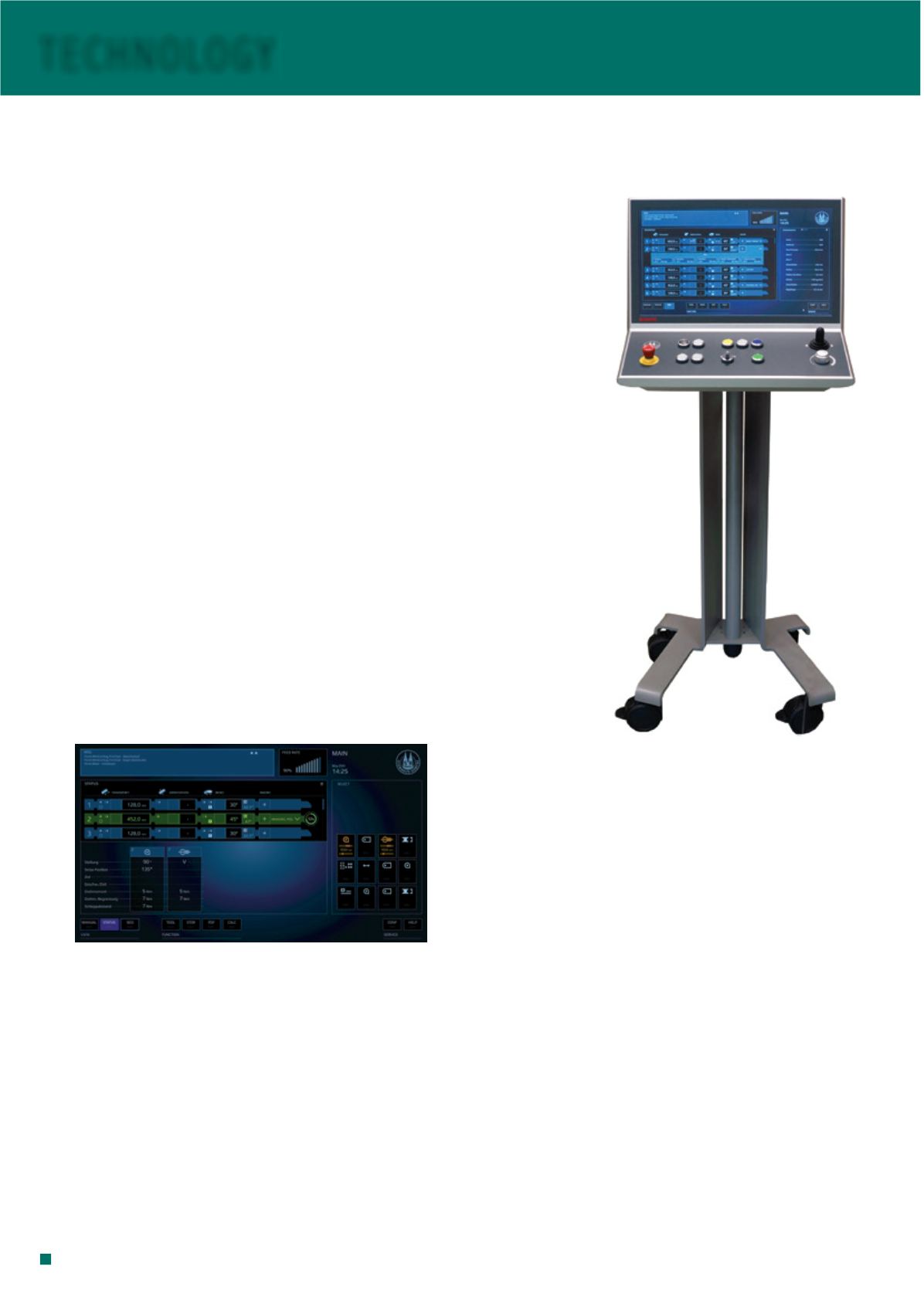
26
J
uly
2016
T E CHNOLOG Y
Bending machine fit for Industry 4.0
INCREASINGLY sophisticated pro-
cesses and the continuous trend for
on-demand production characterise the
new tube bending manufacturing, with
complex geometries of components,
new materials and the call for lower unit
costs and the simultaneously rapidly
changing batch sizes. Production
planners must adapt to this situation,
and this ultimately increases the
demands on machine operators, who
must implement changes reliably.
Schwarze-Robitec
has
reacted
to these developments with a new
operating concept and the integration
of new functions in its CNC-controlled
bending systems.
As a further development of the NxG
control system for bending machines,
which was presented last year, NxG
2.0 simplifies and focuses on the
essentials of the operating concept and
new opportunities in the networking
of bending machines, with increased
flexibility in the production of bending
products.
In order to make the bending
technology fit for ‘Industry 4.0’, basic
modules were integrated into the NxG
2.0 controller. In addition to the standard
statistics on bent components, process
data can be gathered and evaluated.
Integrated sensors provide information
on wear values or, for example, the
consumption of lubricants, and allow
conclusions to be drawn about the
expected bending result, the state
of the bending tools or the need for
maintenance of the machine. This
process data is backed up on the
corporate network or in the cloud. The
data is collected at a central location
and can be retrieved and analysed in
strict compliance with data protection.
Statistical information is viewed in real
time. The state of the machine and
the degree of wear of the tools are
permanently transparent.
The HMI control panel has also
been further optimised. The advanced
software with icon interface provides
high process reliability and intuitive
operation. All operations are clearly
arranged and structured. For example,
the user finds stylised, meaningful
icons for different categories, such
as parameters for dimensions, the
transport, the tool clamping or guide
rails.
“This makes the development of
bending programs or the input of tool
data easier,” explained Bert Zorn,
managing director of
Schwarze-Robitec.
“Moreover, all entries
are always inspected
for validity, therefore
conflicting inputs are
prevented.”
The
CNC
NxT
2.0 also includes an
advanced user manage-
ment system.
This allows the assign-
ment of different user-
levels to employees, from the operation
of the tube bending production to
complex processes such as production
planning, bending equipment and
optimisation of the product, or integration
into the company’s infrastructure.
Schwarze-Robitec GmbH
– Germany
Fax: +49 221 89008 9920
Email:
sales@schwarze-robitec.comWebsite:
www.schwarze-robitec.comTrolley-type machine for belt grinding
and finishing rollers and tubes
GRIND Master offers a trolley-type
machine for diameter grinding of rollers
used in textile machines such as washing
machines, dying machines and bleaching
machines. Finishes up to 0.1Ra can be
achieved, and the machine is designed
to belt grind rollers from 130 to 400mm in
diameter and 1,600 to 3,600mm in length.
This machine features weldment sensing
and grinding along the length. The
diameter finishing ensures no deposit
of colour/bleach on the roller during
operation. The machine is equipped with
an advanced Nanofinish control system
for easy operational control, and there is
also provision for a camera system for
remote observation.
Grind Master Machines Pvt Ltd
– India
Email:
sales@grindmaster.co.inWebsite:
www.grindmaster.co.inProcess
data can be
gathered and
evaluated