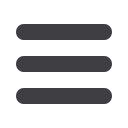

132
S
eptember
2009
www.read-tpt.com›
using solid 8-node hexahedral elements. To simulate the action
of the boost die, an axial pressure was applied directly to the end
of the tube cross section. As shown in Figure 1, a half model was
used instead of a whole model to take advantage of symmetry and
thus reduce computation time. The maximum allowed boost load
at different bending angles was determined using a series of FEA
models, and the effect of the boost load schedule on bending results
was also investigated.
Figure 1
:
Finite element model setup of boost tube bending process
To start the tube bending process, the head of the tube is forced
against the bend die by the clamp die. Then the pressure die
translates to contact the tube OD surface with a fixed amount of load
applied. Once the position of the pressure die is locked, the bend die
and the clamp die rotate to bend the tube. In this example, bending
processes with and
without a boost load
applied were simulated.
The position of the
pressure die is locked
during the entire
bending process.
A typical cross section of a tube is shown in Figure 2. The ovality
ratio, the OD wall thinning ratio, and the ID wall thickening ratio
are the three important parameters to characterise the geometric
quality of the bend. These three parameters are calculated using
the following equations:
Ovality Ratio = Vertical OD – 1.0
(1)
Horizontal OD
OD Wall Thinning Ratio = Original Wall Thickness – Final Wall Thickness
(2)
Original Wall Thickness
ID Wall Thickening Ratio = Final Wall Thickness – Original Wall Thickness
(3)
Original Wall Thickness
Where vertical OD and horizontal OD are shown in Figure 2.
For a tube bending process that uses a boost load, the magnitude
and timing of the boost load affect the wall thinning ratio at the
outside of the bend significantly. Higher boost load leads to less
OD wall thinning and higher ID wall thickening. However, too much
boost load may cause tube buckling, or the tube may detach from
contacting the bend die, as shown in Figure 3. The maximum
allowable boost load at a specific bend angle is defined as the
highest load that can be applied without causing a bend defect,
such as tube detachment from the bend die or buckling. At different
bend angles the maximum allowed boost loads are different. For
example, it becomes increasingly easier to detach the tube from
the bend die as the bend progresses, so the boost load must be
decreased during bending. The maximum allowable boost loads
during the bending process were determined by a series of FEA
models. An acceptable boost load schedule in terms of the bend
die rotational angle that is predicted to minimise OD wall thinning
is plotted in Figure 4. The relative boost load is defined as the ratio
of the axial boost load pressure to the yield strength of the tube
material, so that this schedule could be used for other steel grades
that may have different yield strengths.
Using the boost load schedule shown in Figure 4, two FEA models
were simulated with two bend die geometries. One bend die is
referenced as the original bend die, and the other is referred to as the
Figure 2
:
Ovality
calculation using cross
section dimensions of
a bent tube
Figure 3
:
Determination of the maximum final boost load
Boost
Load
Pressure Die
Clamp Die
Bend Die
Symmetric Plane
Rotation
Bend Die
Boost Load
Tube Detaching
from Bend Die
Figure 5
:
Equivalent plastic strain distribution after bending
Figure 4
:
Optimised boost schedule during tube bending
Bending Angle (Degree)
end of bend
start of bend
Relative Boost Load
0°
90°
180°