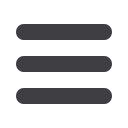

134
S
eptember
2009
www.read-tpt.com›
The FEA simulation indicated that minimum OD wall thinning should
result, by decreasing the boost pressure after the bend arm angle
reaches 66°, and again at 102° and 145°. Trials were completed
using the concept of a declining axial load per the simulation
schedule. Figure 9 shows the load vs bend angle schedule
used in these trials, including the load schedule determined
from simulation.
Making bends
Automatic separation of tools is essential to allow the tube, now bent
to 180°, to be removed from the die. CNC machines particularly
need to be able to easily manipulate the tube after bending. Photo
3 shows the tubing before insertion between the upper and lower
halves of the bending dies.
Wall thinning
Figure 10 reports the OD wall thinning and the ID wall thickening
results for the booster bending trials. Table 1 contains the actual
percentage thinning or thickening values as determined at the specific
bend locations. Photo 4 shows the cross section of sample 10, where
the outer and inner walls of the bend are directly displayed. The
trial data indicates a direct
connection between the
OD wall thinning and the
ID wall thickening. It can
be observed that initially
high boost pressure (up to
102°) provides improved
wall thinning ratios.
Figure 10
:
Percentage wall thickness change data
Ovality
Besides outer wall thinning, ovality and any reduction in cross
sectional area of the tube are important. Ovality was measured at
45° and 125° around the degree of bend and is reported in Table 2.
Ovality is difficult to predict because most wall thinning specifications
include an ovality requirement, in this case < 4%, and a minimum
flow reduction (inside diameter area) of not less than 85%. The
following data indicates that the ratio was satisfactory in samples 10
and 11 but not 9. Sample 9 appears to be an anomaly, most likely
caused by a misaligned clamp die.
Figure 9
:
Axial load settings for booster bending trials
Photo 3
:
Split tooling used for tube bending
Table 1
:
Percentage wall thickness change data
Changes in Wall Thickness
Sample 7
Sample 8
Sample 9
Sample 10
Sample 11
WALL
0%
0%
0%
0%
0%
0%
0%
0%
0%
0%
Bend Arm Angle
0°
1%
1%
1%
7%
-1%
6%
0%
8%
1%
5%
45°
-13% 13%
-7%
23%
-6%
13%
-4%
16%
-3%
15%
90°
-10% 22% -10% 24% -11% 19%
-8%
22%
-8%
24%
135°
-11% 21%
-8%
24%
-9%
19%
-2%
13%
-6%
22%
180°
-5%
4%
2%
3%
-7%
19%
4%
0%
-4%
21%
WALL
1%
3%
4%
1%
1%
-4%
5%
-1%
-1%
9%
Thinning Thickening Thinning Thickening Thinning Thickening Thinning Thickening Thinning Thickening
Photo 4
:
Cross section of
sample No.8 showing the
outer and inner walls of the
tube bend
Bend Angle, Degree
Bend Arm Angle
Wall Thinning & Thickening
sample 7
sample 8
sample 11
FE axial load
Axial Load, lb
Wall Thickness Change, %