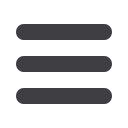

S
eptember
2009
135
›
Deformation Control Technology Inc
– USA
Fax
: +1 440 234 9140
:
sales@deformationcontrol.comWebsite
:
www.deformationcontrol.comPines Technology
– USA
Fax
: +1 440 835 5556
:
info@pinestech.com•
Website
:
www.pinestech.comOvality Data
Sample 9
Sample 10
Sample 11
Angle of Bend
45°
125°
45°
125°
45°
125°
Vertical
1.965 1.925 1.970 1.980 1.970 1.977
Horizontal
2.000 2.035 1.976 1.985 1.980 1.980
Ratio
-2% -6% 0% 0% -1% 0%
Table 2
:
Tube ovality data
Generally, over boosting will cause negative ovality. This condition
exists when the horizontal axis is larger than the vertical.
Conclusion
A comparison of the inner and outer wall thickness change data for
the bend trials in Figure 10 with the model results shown in Figures 6
and 7 shows that the simulation did achieve the objective of reduced
outer wall thinning because of the greater boost load (Figure 9).
However, comparison of Figure 8 predictions for ovality with the
experimental ovality data in Table 2 shows that the simulation load
schedule produced greater ovality than realised in the bend trials.
Using the mentioned 4% limit for ovality, the model boost load
schedule was predicted to produce ovality of about -3.5%, which
is still acceptable but greater than the ovality measured for the trial
bends (ignoring sample 9).
Another simulation was run using a boost load schedule similar to
that of test 8 to compare simulation results against bend tests for
similar boost schedules. A comparison of inner and outer wall thick-
ness changes is shown in Figure 11. For this simulation, the reduced
boost load predicted that the outer wall thinning would be greater
and the inner wall thickening would be less, and this is shown in
Figure 11. Furthermore, the predicted wall thickness changes are in
fair agreement with the measured changes from the bend trials.
It is clear that the model results and the results from the trials
collectively show that:
Boosting changes the ovality direction so that the in-plane
•
(horizontal) tube diameter remains larger than the normal
(vertical) diameter
As the boost load is increased, the amount of outer wall thinning
•
is reduced
However, the boost load must not exceed the load that could
•
cause buckling or separation of the tube from the inner wall of
the bend die. This means that the boost load must decrease as
the bend angle increases.
It is also clear that an accurate model predicts tube bending results
that are sufficiently accurate to be used for process design.
Summary
The study showed that pipe bending could be simulated successfully
given accurate data for the material, interfacial friction, and bending
conditions. Product development time can be reduced considerably
by simulating the process first in order to establish the machine
settings, such as the boost load as a function of bend angle. Getting
close to an acceptable machine/tool set eliminates the trial and error
process that can often prolong downtime during changeovers.
Machines need to be capable of varying booster pressure during the
bend cycle to minimise wall thinning while avoiding tube buckling.
Carriage boosters and normal PDAs do not provide sufficient boost
to overcome the material’s natural yield strength, especially as the
inside wall thickness increases and the force required to deform the
material becomes higher.
Boosting at a high pressure for the first 60° of bend arm provided the
best wall thinning ratio. However, maintaining the boost pressure at
a high level after 102° of bend arm travel has two negative effects:
Firstly, the pipe becomes detached from the die and, if continued,
the booster will push the pipe out of the die completely, and negative
ovality is caused. Pipe detachment from the die was clearly forecast
by the simulation model. In agreement with experience, the model
predicted negative ovality for its higher boost load.
Both machines used in the tests, the Pines No. 4 and the Pines
CNC 150 HD, are designed to bend 4-inch schedule 80 pipe. To
bend pipe of that size with minimal outer wall thinning, it is clear
that a high capacity booster is needed. The Pines No. 4 has a boost
capacity of 25,000 pounds force and the Pines CNC 150 HD has a
boost capability of 30,000 pounds force.
The results of the simulations and subsequent confirmation
that simulation can provide an accurate predictive model are
encouraging. Pines will continue to conduct further tests and
simulations during 2009 when three CNC 250 HD machines,
capable of bending 10-inch schedule 80 pipe, will be tested. The
results will be published as soon as they are available.
Figure 11
:
Comparison of FE simulation results with booster bend trials
Photo 5
:
Cross section
of sample 12 at the bend
location of 45° showing the
outer wall thinning, the inner
wall thickening, and a small
amount of ovalling
Bend Angle, Degrees
Wall Change, Percent