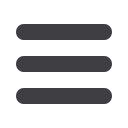

T
echnology
U
pdate
54
S
eptember
2009
www.read-tpt.com›
THE use of composite pipes (PEX-Al-
PEX) has grown to occupy an important
segment in the heating and plumbing pipe
industry. These pipes are available in
different forms according to the installation
conditions. Certain composite pipes require
a protective outer construction, such as a
flexible corrugated pipe or a foam tube.
Composite pipe inserted in a flexible
corrugated pipe is typically placed in cement
foundations and inside walls. Aerial or free
hanging composite pipes are fitted with a
thick foam tube in order to enhance their
insulation properties. Maillefer, Switzerland,
provides complete systems for multilayer
composite pipe manufacturing, and also
delivers lines for producing flexible corru-
gated or foam insulated composite pipes.
For a line configuration that features non-
stop, full-speed production of foam insulated
composite pipe, typical specifications
include entry foam tube lengths from 700 to
1,200m, entry foam tube diameter from 28 to
46mm, entry composite pipe diameter from
16 to 26mm, typical foam tube thickness of
6 or 10mm, maximum bar length of 6m and
a maximum production speed of 35m/min.
The line functions are composed of
five steps: pipe and foam payoff,
foam tube application, seam welding,
jacket extrusion and conditioning in
bars or coils.
Both the foam tube and the composite
pipe are fed to the line using two
single payoffs. To make continuous
production possible, an accumulator is
used when switching from the empty payoff
to the full one. In parallel, the composite
pipe is introduced from another pair of
single payoffs. The pipe is either on coils or
reels. Composite pipe diameters range from
16 to 26mm.
The foam tube is applied around the pipe
by first slicing it open lengthwise, then
merging the pipe into the foam tube. The
cut edges are then heated before being
joined together to form a welded seam. A
compression phase maintains the edges
perfectly aligned and the foam tube is held
in place as the weld solidifies. Finally the
product is ready to receive its outer jacket.
The foam insulated pipe enters the extrusion
head where a medium/high density PE layer
ranging from 0.15 to 0.2mm uniformly seals
the foam tube.
The MXC extruder, coupled with the most
recent screw and barrel innovations, offers
a linear and homogenous melt across the
full RPM range. The nearly finished pipe
then enters a section of cooling water
trough before reaching the conditioning
components of the line.
The product is conditioned either as coils
or bars. Coils are wound on the MWB 1300
Non-stop production of foam insulated
composite pipes for greater protection
fully automatic dual coiler, which features
continuous coiling and strapping with up to
six straps. The pipe being coiled is cut at
predetermined lengths by one of two saw
types, radial or planetary. Both full cuts and
partial circumferential cuts are possible.
Straight bars are fully cut at predetermined
lengths with the radial saw.
The Nomos
®
PSU line control ensures a
precise synchronisation of the various line
operations at the highest possible speeds
for the product. Extruder control and line
speed are optimised for high quality and
minimum scrap.
Advantages offered by composite pipe
manufactured with a foam tube include a
foam insulated pipe that is ready to use; a
perfect alignment of cut edges for a round
product; a complete weld throughout the
full thickness of the foam tube; a fine weld
seam that is barely noticeable; a smooth,
continuous surface from end to end, without
foam tube retraction and wrinkles; and a
product that is sealed with a protective
outer layer.
Maillefer SA
– Switzerland
Fax
: +41 21 691 2143
:
info@maillefer.netWebsite
:
www.mailleferextrusion.com
Cooling of the extruded jacket
Merging the pipe into the foam tube