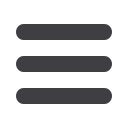

Tube scarf ing systems & tools
www.read-tpt.comM
ay
2015
71
Edge scarfing
equipment
DURATRIM edge scarfing equipment for
welded tube mills, from STE (Superior
Technologies Europe), enables the
manufacturer to trim and clean the steel
coil’s edges as it enters the tube mill
prior to the forming station.
Commercially slit coils can suffer from
as much as 35 per cent of their edges
not being cut cleanly, whether due to
bad practices, poor quality material or
worn tooling.
The result is that edge presentation
at the welding point will be poor, and
welding heat has to be increased to
melt more material. Excessive ‘squeeze
pressure’ also has to be applied to
avoid defects.
These issues will increase material
and energy costs, as well as creating an
excessively large inside/outside welding
flash that then has to be removed.
The Duratrim edge scarfing system
is designed to remove these problems,
and trims the strip edges at the required
rate, ensuring clean and parallel faces
meet at the welding station.
Clamed benefits of
this process include
reduced welding energy;
consistent homogeneous
weld integrity; reduced
strip width/costs; ability
to weld more challenging
materials; and less OD/
ID welding flash (bead).
A consistent strip width
leads to fewer rejects.
The unit runs dry, without
emulsion.
The ‘floating’ design of the scarfing
assemblies allows the unit to follow the
path of the steel strip while maintaining
positive contact pressure on the
scarfing inserts.
The system uses four sets of special
scarfing inserts, which remove material
from the strip edges, top and bottom.
The inserts are supported and kept in
position by eight pneumatic cylinders,
the pressure of which is adjustable,
enabling different amounts of material to
be removed.
All sets of inserts are mounted on a
floating mechanism, ensuring constant
material removal even with movements
in the strip.
STE also offers a comprehensive
range of welding consumables, including
ferrite cores, impeders, induction coils
and OD/ID scarfing inserts.
Superior Technologies Europe Ltd
–
UK
Fax: +44 1256 47 99 33
Email:
sales@st-europe.co.ukWebsite:
www.st-europe.co.ukTube ID scarfing
systems – ready
for Industry 4.0
ALPHA Metall is among the few
manufacturers of machinery who
supply PLC-controlled production
units for Industry 4.0 tube mills for
communicating with main PLC tube
mill boards.
During recent years Alpha
Metall has installed several PLC-
controlled tube ID scarfing systems
as turnkey projects at well-known
tube manufacturers around the
world.
The tube ID scarfing systems are
state-of-the-art and aim to provide the
best tube ID scarfing results.
They can be installed in all tube mills
and consist of standard items such
as ID scarfing mandrels, impeders,
mounting units and custom-made
parts as a set of tow bars for adapting
to various tube mill distances.
Alpha Metall manufactures all of
the items in its factory in Germany.
Commissioning in the customer’s
factory is also possible with engineers
sharing Alpha Metall’s know-how
during commissioning for excellent
tube ID scarfing results.
Alpha Metall GmbH & Co KG
–
Germany
Fax: +49 6831 506958
Email:
info@alpha-metall.deWebsite:
www.alpha-metall.deThe Duratrim
edge scarfing
equipment
increases yield
and weld quality
ID scarfing
GEM Tool Corp designs, engineers and
manufactures ID scarf and bead rolling
systems. The systems’ design can be
incorporated into most existing tube
mills. The company can also custom
design systems for size ranges down
to 12mm ID. In addition to the scarf
systems, Gem Tool manufactures solid
carbide cutting tools and forming rolls.
Gem Tool Corp
– USA
Fax: +1 414 762 0615
Email:
sales@gemtoolcorp.comWebsite:
www.gemtoolcorp.com