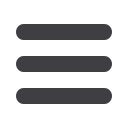

Tube scarf ing systems & tools
www.read-tpt.com74
M
ay
2015
Brushed deburring machine
WHEN using the Spontan high capacity
brushed deburring machine, sawn
precise lengths are placed (manually or
automatically) in the correct position and
axially parallel in the integrated singling
magazine.
The automatic deburring machine
is suitable for two-sided deburring of
round pipes (inside and outside) and
bar sections in one process. Two driver
discs are responsible for singling the
material and for transport during the
deburring process. The discs are each
produced for 6, 12 or 18 material holders
(depending on pipe diameter).
The workpiece rotates in itself and
is transported at four points past the
rotating roller wire brushes so that it
is deburred simultaneously inside and
outside in one process (optionally only
inside/outside). The disc conveying
mechanism is driven by a variable speed
drive. The driver discs are separately
mounted and driven by a spline shaft
with a frequency controlled three-
phase gear motor. Depending on the
length of the workpieces, the adjustable
brush unit is adjusted by sliding on the
machine frame and clamped in position.
The disc drive motor has 0.37kW output.
Spontan
– Germany
Website:
www.spontan.euInside tube scarfing systems
REQUIREMENTS such as cost
savings and emission reductions are
gaining increasing relevance in the
pipe producing industry and in plant
construction.As a producer of inside tube
scarfing systems, Ernst Blissenbach
GmbH offers a high level of safety for
demanding pipe production processes.
BLISSart
®
tools are synonymous with
stability, longevity and functionality.
Their construction offers a reduction of
tool-related machine downtime, avoids
spiralling costs and improves the quality
of inside tube scarfing.
Each
new
development
or
improvement of a tool is based on
proactive identification of customer
needs. All business processes at Ernst
Blissenbach GmbH are designed around
customer requirements. That is a benefit
of great practical value, as it makes pipe
production progress predictable and
calculable, speeds up processes and
reduces sources of errors. BLISSart
®
seam monitoring, for example, offers a
reliable scarfing control that results in
reduced scrap rates. This symbiosis of
technical innovation and intensive tool
and process research is what makes this
company so successful. Blissenbach
aims to be a global trendsetter when
it comes to optimising pipe production
standards.
The company also applies innovation
to its internal work processes. This led
the company to expand its machinery,
thus increasing manufacturing capacity.
This expansion did not only involve
modernising the production facilities
and hiring new employees but also
improving the flexibility and quality of
production. “With the expansions, we
are now working at the highest level
and can be even more efficient when
it comes to addressing the individual
wishes of customers. There is simply no
limit to further innovative development of
solutions,” Ernst Blissenbach explained.
He added: “Everybody wants to develop
something special – we managed to do
that and continue to do that.”
The company believes that being
innovative does not just mean refining
the details, it means always being willing
to find future-orientated solutions.
Ernst Blissenbach GmbH
– Germany
Email:
info@blissenbach.deWebsite:
www.blissenbach.de