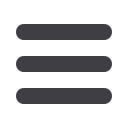

109
J
uly
/A
ugust
2007
sizes and steel grades. There is also a better yield, with improved
quality in the shape of the tube end leading to a reduction in
cropping.
Because of a wider wall thickness range capability on the same
mandrel, the total number of mandrels required to cover the
complete size range is reduced. Consequently, there is a reduced
mandrel inventory and less frequent mandrel size changeover.
There is also a significantly reduced consumption of mandrels and
rolls because of lower average and peak pressures.
There is a higher degree of stability of the material flow during
rolling, which reduces accidents and the losses for cobbles. This
increase in efficiency leads to better productivity and yield.
4. Technical profile of the
FQM™ retained mandrel mill
The FQM™ mill is mainly comprised of
rolling units and cartridges – each one
with 3 driven rolls – supported by chocks
and mounted in a shifting slide inside the
cartridge. Each cartridge is comprised of
two cast shells. The design of the cartridge
allows the radial extraction of the shifting
slides, containing chocks and rolls, without
the necessity to open the cartridges into
two halves.
Due to the geometry of the mill the
required adjustment to roll position before
or after profile redressing can be undertaken directly with the
hydraulic capsule. The hydraulic capsules are mounted outside
the container and engaged/disengaged to the roll during the roll
changeover procedure.
The mandrel supporting units are installed inside the container.
These units guarantee optimum operation, by means of three self-
centring rolls, with adjustable positioning in accordance to mandrel
size, and oil-hydraulically operated for opening/closing the mandrel
centring and support during rolling.
The number and position of mandrel supporting stands depends on
the mill configuration. For example, on a 5-stand mill the mandrel
supporting stands are installed at the inlet and outlet of the first
rolling unit, between the third and the fourth rolling unit and at the
outlet of the last rolling unit.
The roll cartridges and the mandrel supporting units are inserted in
a fixed and rigid cylindrical container and sit on side supports inside
the container. Due to his geometry the container is designed to react
uniformly to the three separating forces acting in radial direction.
For the roll changeover all the rolling units and the mandrel
supporting units are pushed along the rolling axis toward the mill
exit. The changeover is performed with a side-shifting type car.
5. FQM™ process control
Seamless tube plants are configured as distinct technological
areas in which different jobs can take place at the same time.
Each technological area has its own process control system that
is integrated with the others via level 3 automation. The following
goals can be achieved with this process control system:
• Enhanced dimensional quality of the final product
• Improved operator independence for better production quality
• Improved consistency of production quality
• Maximised yield of the plant
• Simplified start-up for new production configurations
A suitable integration and process automation system is essential
to match the high quality performance and results gained from 3-roll
pass design. The Danieli automation system is supported by ‘fast’
data collection of the main process variables. During the rolling
process all data is gathered from level 1 and used for process
tracking, process tuning and input for level 2 models.
›
Figure 6
:
Advantages of the FQM process: comparison between 2-roll RMM (left) and 3-roll FQM (right)
fi
Figure 7
:
A mandrel supporting stand from the FQM container