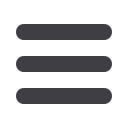

110
J
uly
/A
ugust
2007
5.1 Major system features
Master speed control enables the coordinated increase and
decrease of motor speed references. This speed control is carried
out by always ensuring comparative balance of the set drive speeds
during the rolling process.
An essential element of the system is wall thickness measurement;
gauging of the thickness of the rolled material is provided and the
set of the proper roll gap opening performed. The process control
system analyses the data produced by the wall thickness gauge
located at the extractor stand exit. Based on the results, the mill
mathematical model updates the speed and gap parameter set
points to improve the quality of the rolled pipes.
Impact drop compensation acts to minimise the length
of pipe rolled at speeds that are different from pre-set
values by using auto-adaptive parameters, relying on
real-time calculation algorithms.
The core of the process control is the installation of
hydraulic capsules, which are fully managed by the
system. On each roll cartridge three independent
hydraulic capsules are mounted, one per roll. The main
function of the control system of the hydraulic capsules,
controlled by servo-valves, is to move the stand rolls.
The position of the cylinders and pressure of the chambers
are measured in real time by dedicated transducers and
used by a dedicated high-speed control system, capable
of controlling and maintaining the set position.
5.2 Control system functions
• Synchronised position control maintains the symmetry between
rolls and the rolling centreline, to avoid damages to chocks and
bearings
• Separation force measurement computes the average and
differential values of the rolling forces using the pressure
transducers installed on the hydraulic capsules
• Capsule position control regulates the position of the rolls by
comparing position pre-set and position feedback and set-up
for roll changeover
• During rolling, automatic variation of the roll positioning
takes place in accordance with a calculated rule, in order to
compensate the temperature disuniformity over the tube length
• Impact compensation increases the gap between the rolls
during the entrance of the shell into each stand, thus reducing
excessive thickness on the tube head end. The impact peak
compensation on mechanical components limits the stress
on the roll bearings and reduces the mandrel and rolls
consumption
• A general damage prevention system (automatic roll emergency
opening), based on automatic gap increase, limits the overload
and enables the tube end to be rolled. There is also an
emergency capsules control to avoid strong deformation of the
pipe and consequent damage to mechanical parts, mandrel
and rolls
6. FQM™ integration in the rolling line
A typical material flow, together with the process control installed,
is a central part of the system. The billet, cut into multiple lengths
of the rolling length, are re-heated to 1,280°C in the re-heating
furnace, rotary hearth type or walking beam type.
After the re-heating, the piercing of the billet is undertaken in a cross
rolling mill to form a round hollow shell. The cross rolling mill mainly
consists of two opposite and equi-rotating rolls, suitably shaped in
order to rotate and advance the billet against a plug. The external
deformation of the material is contained by means of lateral rotating
disks or fixed shoes (at 90° in respect to the rolls). The internal plug
determines the internal material deformation.
The cone shape and divergent orientation of the work rolls require
no abrupt change of ovality and twist direction of the material during
rolling. They help achieve the following benefits:
fi
Figure 10
:
Material flow during rolling in a 5-stand FQM
›
Figure 8 and 9
:
A side view of a 5-stand FQM (top and above)