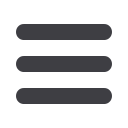

wire
treatment
Wire & Cable ASIA – September/October 2007
131
Kieselstein – making life easier
Kieselstein has improved the innovative technology of draw-peeling of wire.
The basis for this improvement is increasing quality requirements to the final
products, for example highly stressed springs used in the automotive sector. The
steel wire those springs are made of needs to show a high degree of pureness
and chemical composition.
The draw-peeling of wire allows the creation of a very smooth surface of the wire,
achieved by the continuous removal of the outer layers of the surface by one
closed, circular, fixed tool. This avoids the typical grooving that appears with the
usage of several blades during other processing methods. After the draw-peeling
process the wire surface neither needs to be hardened, nor requires any polishing
or grinding.
Besides valve spring wire and steel wire, aluminium, copper, nickel alloy and
different special materials can be draw-peeled.
One of the milestones in the development of this procedure and the respective
machine technology is the modular type series of high-speed draw-peeling-
machines. Emanating from existing machines, a new modular concept has been
developed which allows an especially gentle processing improving the quality of
the finished wire.
At the same time a considerable gain in productivity is reached due to an increase
of the draw-peeling speed. Due to the modular concept the machines can be
composed according to the customer’s individual requirements.
Kieselstein International GmbH – Germany
Fax
: +49 371 910 4105
:
info@kieselstein-group.comWebsite
:
www.kieselstein-group.comCovering all the steps
Niehoff has developed production
equipment which covers all steps
from copper wire drawing to cable
manufacturing. For copper wire
annealing, the RM type continuous
annealers are a standard solution,
while the RI type inductive con-
tinuous annealers are designed
for wires made of metals with low
electrical and thermal conductivity.
The
contactless
annealing
method is particularly well suited
for copper alloys such as brass,
bronze, German silver and also
for nickel and nickel alloys. It can
also be used for wires of copper,
tin-plated copper or silver-plated
copper, precious metals and their
alloys, as well as for composite
wire and special material wires.
Compared with annealing in a
bell furnace, continuous induction
annealing causes the same wire
material and at least equivalent
mechanical properties. As the
grain size is very fine, tensile
strength and yield limit are up to
30N/mm² higher, and elongation is
the same or higher.
The RI type annealers are designed
for round wires in the wire diameter
range of 0.15 to 4.5mm.
The Niehoff-Steuler WPT wire
plating technology for tin plating,
silver plating, nickel plating, zinc
plating, and alloy-plating of copper
and other non-ferrous metal wires
benefits from the experience of
Niehoff and Steuler Anlagenbau.
Maschinenfabrik Niehoff GmbH
& Co KG
Fax
+49 9122 977 155
:
info@niehoff.deWebsite
:
www.niehoff.deRI type annealer
❍
Induction heating technologies at Celes
The Celes Group has been involved in most induction heating technologies in
heat treatment for steel wires and cables. As well as designing, manufacturing
and commissioning solid state inverters for high or middle frequency induction
heating, cooling systems for industrial facilities include:
recycling groups with plate exchangers, refrigerated unit, cooling towers or air
cooling unit
filtering and recycling groups for quenching unit
quenching tanks (water with or without additives or oil coolant) equipped with
propeller pumps and immersed cooling exchangers
Inductors
can
also
be
specifically designed for various
and complex applications. In
the field of wires and cables,
Celes is involved in the
following field of activities:
Celine
high-flux
induction
heating of round or square
billets and tubes. Celine
technology is characterised
by power density of 4-6Mw/
m², ie up to six times that
of traditional inductors, an
electrical efficiency of 85%
above the Curie-point, as
opposed to the previous 50-60%, representing a considerable saving in electrical
energy consumption, a space requirement limited to approximately 1m per
MW injected in the typical case of a billet of 90mm in diameter, thermal and
mechanical protection devices designed to reduce maintenance costs when
operating under extreme conditions.
Celes – France
Fax
: +33 038976 3679
:
info@celes.frWebsite
:
www.celes.com•
•
•
Oil quenching of threads from Celes
❍