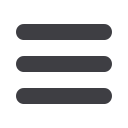

10
AFRICAN FUSION
March 2017
SAIWmember profile: HC Heat Exchangers
H
C Heat-Exchangers (HCHE) is
a design and manufacturing
company specialising in the
manufacture of heating, ventilation, air
conditioning and refrigeration equip-
ment. Started in the 1970s as the Heat-
ing Centre group, the company traded
under the German Günter SA banner
from 1995 until Günter’s withdrawal
fromSouthAfrica in 2001, afterwhichHC
Heat-Exchangers was established as an
entirely South African-owned company.
Today, HCHE is the largest manu-
facturer of finned-tube heat exchang-
ers in southern Africa, serving both the
commercial and industrial market seg-
ments. The equipment range produced
comprises commercial refrigeration
products through to large custom-built
units for industrial applications.
“We produce condensers, evapora-
tors – both flooded and direct expan-
sion –chilledwater coils, hot water coils,
steam coils and dry coolers. We offer a
variety of different constructionmateri-
als to suit all operating environments
including all-stainless coils designed
and manufactured to SANS 347 and
ASME B31-5 specifications and welded
according to ISO 3834 Part 2 quality re-
quirements,” Banza tells
African Fusion
.
From an original 2 500 m
2
facility,
HCHE has rapidly expanded and is al-
ready looking to expand on its 16 000m
2
production facility inElandsfontein, east
of Johannesburg.
“We moved into these premises at
the start of 2015with almost 300 people.
We are nownearing 350 and are looking
for additional space next door. We have
added a newHVACdivision toour facility
in order to handle specialised products
such as rooftop air-handling units and
we have recently launched a product
called the Dew Maker, which extracts
drinking water from the air. We design
all of our products with sustainability
in mind,” Banza says.
Based on an assessment carried out on
December 1, 2016, HC Heat Exchangers’
workshop in Elandsfontein, Gauteng, was
certified under the IIWManufacturer Certi-
fication Scheme for the management of
quality inwelding inaccordancewith
ISO 3834 Part 2 – Comprehensive
Quality Requirements.
African
Fusion
talks to Hans Banza,
the company’s responsible
welding coordinator.
One of the biggest stainless steel
products HCHE has manufactured thus far, an
890 kW spiral freezer manufactured by the compa
to freeze poultry products.
Hans Banza (third from left) receives a Sassda Columbus Stainless award on behalf of HC Heat
Exchangers: from left: Charles Cammell, chairman of Sassda; Shannon Freeman, Jaguar Stainless
Steel; Hans Banza, HC Heat Exchangers; and John Tarboton, executive director of Sassda.
HC Heat Exchangers
exceeds challenging
HC-branded systems are used by
supermarkets suchCheckers Hyperama,
Shoprite, Pick n’ Pay and Spar. Other
project successes include the Mall of
Africa, Logico Swaziland, Bluff Meat
Supply and Aramex.
“We continue to produce products
customised froma standard platformto
ensure consistency in the quality of the
delivered product. With our expansive
industry knowledge and a clear under-
standing of our customers’ applications,
we deliver products tailored to their
exact requirements – always striving
towards anoptimisedsolution,”headds.
Success at the Stainless Awards
HC Heat Exchangers was a joint run-
ner up in two categories of the Sassda
Columbus Stainless Awards in 2016: the
Food and Beverage category and the
Engineering category.
The Food and Beverage accolade
was awarded for oneof thebiggest stain-
less steel products HCHE has manufac-
tured thus far, an 890 kW spiral freezer
manufactured by the company to freeze
poultry products. The unit, constructed
almost entirely from 304 stainless steel,
with only the fins and fan panels being
made from aluminium, is designed to
freeze over 10 t of poultry per hour. Cold
air leaves the heat exchanger at -34° C
and is blown into a 10mhigh cylindrical
room, which contains the conveyer car-
rying the poultry. As the product passes
through the system it is quickly frozen
and packaged.
One of the key challenges faced in