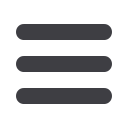

Automated Wire
Production
51
Wire & Cable ASIA – January/February 2007
“Well begun is half done,”
the old adage tells us
I
n wire making, well begun is
all
done – and certified as
perfect, and delivered to a satisfied customer who pays
a good price, without demur. The key to this happy state
of affairs is automation.
Wire making has always been an exceptionally
streamlined operation, in the context of its times. With
the advent of the PLC — programmable logic controller
— and its fulfilled promise of tight control of the process,
the modern wire maker is able to achieve efficiencies on
the grand scale.
Synchronisation of the flow of inputs from sensors with
the flow of outputs to actuators is technical language.
But there is nothing difficult to understand about the
very real-world benefit this measure of automation confers: an edge of competitiveness in a global
market in which an edge can mean the difference between a front-runner and an also-ran.
The companies showcased in this section are run by professionals thoroughly familiar with
continuous-flow production conducted by means of preset instruction. The equipment and services
they offer are for those who recognise the value of that degree of automation in wire making.
OMA also supplies turnkey plants
for the manufacturing of rubber and
plastic hose. The product range
also includes vertical and horizontal
axis braiding machines with single
or multiple decks; automatic and
semi-automatic winding machines;
coiling machines and pay-off creels
for braiding lines, extruders and
drawing machines; taping machines
for rubber, polyethylene, copper
and aluminium tapes; wrapping/
unwrapping machines for rubber
hoses and cables; spiralling machines
for textile and metallic yarns;
complete lines for the production of
rigid mandrel hoses; and ancillary
machines for the production of rubber
and thermoplastic hoses and cables.
Formed in Italy in 1957, OMA now has
two branches and a representative
office – OMA USA, OMA UK and the
recently opened OMA Srl, Shanghai
representative office.
A vast network of agents and
distributors in more than 50 countries
provide telephone and on-site
assistance, quick delivery of spare
parts and technical consultation.
Exporting more than 80% of its
products around the world, OMA Srl
often collaborates with customers
for special product development
programmes, either at its own facilities
or at customers’ plants.
OMA Srl – Italy
Fax
: +39 039 6084571
:
oma@omabraid.itWebsite
:
www.omabraid.comOMA Srl specialises in the manu-
facturing of braiding and winding
equipment for the reinforcing of
rubber, thermoplastic, PTFE, metal
bellow hoses and electric cables, as
well as for a great variety of textile
products, from small ropes to many
kinds of round, tubular or flat braids
and medical products.
Photo credit:
Fine International
New office strengthens OMA
The Type 140 V braiding machine from OMA
▼