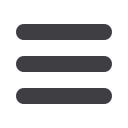

18
AFRICAN FUSION
March 2015
Phased-array ultrasonic testing (UT)
U
nexpected failure of small bore pipingwelds is a recur-
ring problem at nuclear power plants. In fact, socket
welds account for more than 80% of weld failure in
nuclear plants. Due to the lack of reliable inspectionmethods,
in addition to the large number of welds, socket welds are not
subjected tovolumetric inspectionona regular basis. However,
socket weld cracking has caused unplanned plant shutdowns
in several nuclear plants. The losses incurred by unplanned
shutdowns are significant; consequently, early crack initia-
tion and crack detection, including the detection of fillet weld
manufacturing defects, is of the utmost importance.
Current inspection techniques are not capable of reli-
ably inspecting socket welds, therefore new approaches are
needed. The new technique must be sensitive to socket weld
cracking, which usually initiates from the triple point, in order
to detect the cracking during the early failure phase.
In this study, shear wave phased array ultrasonic inspec-
tion techniques are applied to increase inspection speed and
reliability. Additionally, a manually encoded scanner has
been developed to enhance contact conditions and maintain
constant signal quality.
Introduction
Failure of small bore piping socket welds installed in a nuclear
power plant is a recurring problem. Although not a severe
safety issue, it may cause an unexpected shutdown of power
plant operation to repair the damage, which leads not only to
economic loss but also to serious impacts on the operation of
the power plant. To date, small bore piping socket weld dam-
age has been extensively reported globally. For US nuclear
power plants in the 1990s, the small bore piping accounted for
80% of 450 piping-related failures, and accordingly has been
considered and managed as an important factor in operating
nuclear power plants.
In the case of Korea’s nuclear power plants, since the leak-
age in a drain line piping socket weld of a steam generator
in Kori Nuclear Power Plant, Unit 3, in 2008, a management
programme for the small bore piping socket welds presently
installed in nuclear power plants has been established to
implement ultrasonic inspection for volumetric examination
as an addition to the surface examination requirements speci-
fied by ASME Section XI.
With the ultrasonic inspection currently being applied,
however, inspectors experience difficulties in contacting the
ultrasonic probe evenly owing to small installation space of
the piping, limited access by examiners, and the small diam-
eter of small-bore piping. Inspection has not, therefore, been
implemented properly due to restricted access by the probe
and interference with neighbouring structures.
In this study, a shear wave phased array ultrasonic probe
was designed andmanufactured and amanual encoder scan-
nerwas developed inorder to solve theproblemof accessibility
to the weld leg of the small bore piping socket welds by the
ultrasonic beam. Additionally, an experiment to detect flaws
on a specimen with fatigue cracks was carried out using the
manufactured probe to develop a reliable inspection technol-
ogy for small bore piping socket welds.
Development of inspection technology
In general, shear waves have shorter wavelengths compared
to longitudinal ultrasonic waves and are sensitive to various
material properties such as grain size and structural charac-
teristics, while having a relatively low level of penetration into
thematerial. However, thiswave type offers good sensitivity in
contrast to the penetration offsets for carbon steel or stainless
steel, and as a result a shear wave mode is generated and ap-
plied for general ultrasonic testing. Nevertheless, in order to
generate a shear wave for an object to be subjected to phased
array ultrasonic inspection, which has recently attracted
attention, as well as normal ultrasonic inspection, a wedge
manufacturedwithdue considerationof Snell’s law is attached
to the front of the probe. But the attachment of the wedge at
the time of small bore piping socket weld inspection
may widen the gap between the inspection area and
the index point of the probe, and thereby cause poor
accessibility, which in turn is likely to decrease flaw
detection capability.
The phased array ultrasonic probe can create
a beam that is incident to a certain angle without
using a wedge. For this reason, considering design
parameters of a phased array ultrasonic probe, a
shear wave ultrasonic probe was designed to gen-
Small bore pipe socket weld inspection
using phased-array UT
Byungsik Yoon*, Yongsik Kim and Jeongseok Lee
At the 67
th
IIW International Assembly and Conference, a team from the Korea Hydro
and Nuclear Power (KHNP) Central Research Institute presented this paper about the
use of phased-array ultrasonic testing (UT) for small bore pipe socket welds on nuclear
power plants.
Figure 1: The access offset caused by a phased array probe wedge for small bore
piping, (a) with wedge, (b) without wedge.