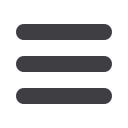

19
March 2015
AFRICAN FUSION
erate an effective shear wave within the range of the total
refraction angle.
This study considered the probe design parameters indi-
vidually with the aim of designing a shear wave phased array
ultrasonic probe for socket weld inspection. First, the frequen-
cy was set at 3.5 Mhz, which is suitable for general stainless
steel inspection, and the number of piezoelectric elements
was set at 16. Efforts to minimise the pitch of the probe and
radius mode transmitted along a vibrator of the probe were
made in this study. As a consequence, each piezoelectric ele-
ment, when vibrating, can be independent from surrounding
elements. Therefore, itwas designed togenerate a strong shear
wave at the edge of the piezoelectric element. Furthermore,
the piezoelectric element was designed to be smaller than the
wavelength so as to vibrate as a single point source.
The parameters of the selected shear wave phased array
ultrasonic probe are shown in Table 1.
When the probe is manufactured using the selected pa-
rameters, the side lobe or grating lobe should be eliminated
or minimised at the used inspection angle.
The grating lobe occurring in the phased array ultrasonic
probe is caused by constructive interference made by sur-
rounding piezoelectric elements that have identical phases
and different time delays. In other words, this happens at an
angle where delays match each other periodically and when
signals are inphase at a refraction angle. Inparticular, a grating
lobe whose beam is wide and highly sensitive is an important
factor that shouldbe considered in the phased array ultrasonic
probe design.
Figure 2 shows the directivity for each angle calculated
based on parameters in Table 1. The figure indicates that there
is interference with themain beamat each refraction angle or
in the absence of an adjacent sound beam. Relatively small
side lobes were expected not to have an effect on the inspec-
tion signal, although they are present onboth sides of themain
beam. As seen in the directivity plot, as the angle increases,
the size of the main beam decreases and the angle at which
the main beam is generated becomes wide. The directivity
illustrated in Figure 2 is the result of concentrating at a depth
of 40 mm from the probe surface.
Manual encoded scanner
As small-bore piping socket welds are thin and the weld
leg widens the gap between the probe index point and the
inspection region of interest, the beam arrives at a distance
of approximately two to three skips, instead of one skip. As
a result, multiple reflection results in a complex signal, thus
making it difficult to clearly investigate flaws with a real-time
S-scan. Furthermore, in a narrow inspection space, the test
instrument should be checked and inspection should be
made simultaneously while maintaining contact between
the small phased array ultrasonic probe and the small bore
piping. Therefore, an inspector cannot concentrate on evalu-
ation, which leads to low reliability of the inspection.
To solve these problems, this study developed a ring-type
scanner with which the probe could be fixed and clamped to
the external diameter of small-bore piping. The scanner is
clamped to piping in the form of two connected semicircles
with an angle of 180
°
, and it adjusts the contact force of
the probe and revolves in the circumferential direction. A
micro-encoder that transmits the circumferential location
of the probe to the phased array ultrasonic test instrument
Parameter
Design Value
Frequency
3.5 MHz
No. of elements in primary axis
16
Primary axis pitch
0.3 mm
Inter element spacing
0.1 mm
Width of element
7.0 mm
Total active length
9.5 mm
Table1: Phased array probe specification.
Figure 2: Directivity plot for steering angle at 40 mm in front of Elements 4:
Experiment Apparatus and Method.
was attached. Figure 3 displays the manufactured manual
scanner developed in this study with its design.
Flawed specimen
In this study, flawed spec-
imensweredesignedand
manufactured todevelop
the inspection technique.
The material of the fa-
tigue crack specimen is
304 stainless steel and
two specimens with leg
length of 1:1 and 1:2were
designed and manufac-
tured with socket weld
piping with a 1.0″ nomi-
nal diameter. Figure 4
shows themanufactured
flawed socket weld specimens.
For the flawed specimens, the typically occurring types of
flaw in the socket welds were analysed. Three flaws were de-
signed to be included into one specimen for the flawed speci-
PA probe
Probe fixture
Encoder
Tension adjuster
Figure 3: Hand driving manual encoded scanner for small-bore socket weld
piping.
Figure 4: Photo of manufactured flawed
socket weld specimens.