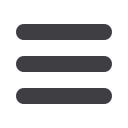

Microstructural study of turbine rotors
AFRICAN FUSION
March 2015
24
T
rial weld joints were made using a special station for
welding large forgings of up to 135 tonnes in weight
for use in the production of combined rotors for steam
power plants. The hot wire GTAW process was applied for
joining various low and high-alloyed creep resistant steels
(28CrMoV 4-9, 27NiCrMoV 15-6, COST F andCOST FB2). Different
filler metals together with the application of interlayers were
used for individual weldments and the best variants were se-
lected on the basis of mechanical testing andmicrostructural
investigations.
Weld joint designed for creep conditions underwent creep
testing at temperatures up to 650
°
C. Fracture surfaces of
ruptured cross-weld specimens were analysed using a scan-
ning electron microscope, and microstructures of individual
zones of weldments were investigated using methods of light
scanning and transmission electron microscopy. The critical
zones were determined from a point of view of creep failure
in relation to temperature and stress conditions.
Introduction
Large rotors for fossil fired power plants are produced as one
piece from a huge ingot. Their weight is very high and it is dif-
ficult to forge such big components and subsequently carry
out heat treatment. In addition, different material properties
are desired for high-pressure, intermediate and low-pressure
parts of these rotors, which are exposed to different steam
conditions. All these disadvantages can be solved by adopt-
ing combined rotor designs, which consist of several parts
made of different steels. Individual pieces can be heat treated
separately, joined together by welding and then heat treated
in special furnaces separated by walls. Using this technology,
the properties of the rotor gradually change between the low
pressure and the high pressure parts.
The weld joints, however, are usually susceptible to pre-
mature failure. Therefore, the selection of the base materials
andconsumables, aswell as theweldingprocess andpostweld
heat treatments have to be optimised based on the results of
proper weld joint testing.
The paper deals with investigations involving several trial
weld joints, which are designed for production of combined
rotors for fossil fuel power plants using a special station for
automaticwelding of large forgings up to 135 tonnes inweight.
Creep resistant low alloyed as well as new high chromium
steels for applications at ultra-supercritical conditions, which
were developed within the frame of the European COST pro-
grammes [1], were used for the production of the trial welds.
Welding procedures and experimental
materials
Several similar and dissimilar weld jointswere produced using
the sameweldingmethod – hot wire gas tungsten arc welding
(GTAW) into a narrow gap. Low alloyed and creep-resistant
high chromium steels were used as the base materials. Two
discs of the basematerials with a diameter of about 600mm, a
length of 200mmand a wall thickness of 120mmwere joined
together using different consumables. Welding was carried
out in the PC position – around the vertical longitudinal axis
of the discs. A list of the trial weld joints and materials used
for their production is given in Table 1. An interlayer was de-
posited on one of the base materials of B and C weld joints
using the above mentioned welding method and special
heat treatments were carried out before the final joints were
completed. Macrostructures of individual weld joints are
shown in Figure 1.
Also delivered at last year’s IIW International Assembly and Conference, this paper
details procedure development for welding turbine rotors for steampower plant using
creep resistant rotor steels and the hot wire GTAW welding process.
Microstructural study of trial weld joints
for steam turbine rotors
Dagmar Jandová and Josef Kasl: Research and Testing Institute, Czech Republic
Table 1: List of weld joints investigated.
Weld joint
Base material BM1
Base material BM2
Weld metal
Interlayer
Similar weld A
27NiCrMoV 15-6
27NiCrMoV 15-6
NiCrMo 2,5-IG
-
Dissimilar weld B1
27NiCrMoV 15-6
28CrMoNiV 4-9
NiCrMo 2,5-IG
Union I CrMo 910
(2.5Cr1Mo)
Dissimilar weld B2
27NiCrMoV 15-6
28CrMoNiV 4-9
NiCrMo 2,5-IG
P24-IG (2.5Cr1MoVNb)
Dissimilar weld C
27NiCrMoV 15-6
X14CrMoVNbN 10-1
(COST F)
NiCrMo 2,5-IG
P24-IG (2.5Cr1MoVNb)
Dissimilar weld D1
X14CrMoVNbN 10-1
(COST F)
X13CrMoCoVNbN 9-1
(COST FB2)
Thermanit MTS 3
-
Dissimilar weld D2
X14CrMoVNbN 10-1
(COST F)
X13CrMoCoVNbN 9-1
(COST FB2)
Thermanit MTS 616
-