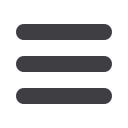

Microstructural study of turbine rotors
AFRICAN FUSION
March 2015
26
steel and different interlayers were investigated – B1 and B2
weldments with interlayers of 2.5Cr1Mo steel (Union I) and
2.5Cr1MoVNb steel (P24) respectively. The Interlayers were
depositedon the 28CrMoNiVbasematerial. The temperatureof
postweld heat treatment (PWHT) of the variant B2was slightly
higher than that of the B1 variant.
Microstructures as well as mechanical properties of both
variants are similar. Themicrostructure of theweldments cor-
responded to tempered bainite that can be described based
on LM and SEM observations as carbides spread more or less
homogeneously in a ferritic matrix. The density of the carbide
particles was different in individual zones of the weld joint, ie,
it was higher in the base materials than in the weldmetal and
interlayers. The size of precipitates was higher in 28CrMoNiV
base material than in 27NiCrMoV base material. The higher
temperature of tempering in the case of 28CrMoNiV steel was
the cause. No significant coarsening of the structure in the
heat affected zones (HAZ) was observed in either of the base
materials.
Microstructures in of B2 variant were more tempered in
compliance with the rather higher temperature of PWHT in
comparison to the B1 variant. Nevertheless, precipitates in
the P24 interlayer of the B2 weld joint were finer and more
regularly spread than in the Union I interlayer of the B1 weld
joint. In addition, carbon enrichment at the interface of the
interlayer and the weld metal was observed in the B1 variant.
This fact revealed itself in the significantly higher density of
precipitates in the interlayer near the fusion line (Figure 5).
The microstructure of the B2 weld joint seemed to be better
than the B1 weld joint. The crossweld hardness profile (Fig-
ure 6) showed more balanced hardness values in the case of
the B2 variant.
Mechanical tests revealed that the interlayer was the
weakest zone of both theweld variants. Fracture during tensile
tests occurred in central parts of the interlayer. Both B1 and B2
variants satisfiedmechanical requirements. Due to its slightly
better mechanical properties and more favourable micro-
structure, the B2 weld joint was selected for real production.
Dissimilar weld joint C
Themicrostructure of dissimilar weld joint Cof 27NiCrMoV and
COST F steels with NiCrMo2.5 weld metal and P24 interlayers
is very heterogeneous. After PWHT the microstructure of the
COST F base material corresponded to temperedmartensite,
while other parts of the weldment consisted mainly of tem-
pered bainite with possible small amount of martensite in the
27NiCrMoV base material. Seven main zones were observed
in the cross section of the weldment – two base materials
(Figures 7 and 8), three heat affected zones, the interlayer
(Figure 9) and the weld metal (Figure 10). Bands of coarse-
grained and fine-grained structures could be distinguished
within the interlayer and in the weld metal. The structure of
the COST F basematerial unaffected bywelding is significantly
coarser than that of 27NiCrMoV basematerial. Near the fusion
line at the interface between the high-alloyed COST F base
material and the low alloyed P24, carbon enriched bands
were observed. As could be expected, carbon enrichment oc-
curred in the basematerial, which resulted in a local increase
in hardness (Figure 11).
The crossweldhardness profile is shown in Figure 12. Mean
hardnesses of the COST F base material and the weld metal
were the same – 265 HV. Hardness of 220 HV and 300 HV were
Figure 5: LM micrographs of Weld B1 showing a carbon enriched interface between
the weld metal and the interlayer.
Figure 6: The crossweld hardness profile of Weld B after the PWHT: a) B1 variant, b)
B2 variant.
Figure 7: LM micrograph showing the
Bainitic structure in Weld C’s 27NiCrMoV
base material.
Figure 8: LM micrograph of Weld C
showing a tempered martensite of the
COST F base material.
Figure 9: LM micrographs of Weld C showing the Bainitic structures of the
interlayer: a) coarse-grained and b) fine-grained microstructures.
Figure 10: LM micrograph of Weld C
showing the Bainitic structure of the
weld metal.
Figure 11: LM micrograph of the COST F/
P24 base material for Weld C showing
carbon enrichment at the fusion line.
mechanical values for this weld joint were satisfied.
Dissimilar weld joint B
Two variants of the weld joint of 27NiCrMoV and 28CrMoNiV
steelswith the sameweldmetal on thebasisof 2.5Cr0.4Mo2.5Ni