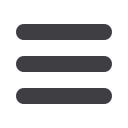

March 2015
AFRICAN FUSION
31
Each structural section is flanged at the ends so that so that the 84 m towers can
be erected onsite by bolting them together.
On the growing line, ESAB roller beds with built in manipulators are used to
support the growing section and the can to be added.
A completed tower section on one of DCD Wind Tower’s four growing line.
rotating rollers and shuffle it along and onto a roller bed
further up the line. A newcan is then loaded andwelded,
before the whole weldment is shuffled up a further
3,0 m. The welding is done using state-of-the-art ESAB
submergedarcweldingequipment, with thewhole tower
section being rotated to complete each circular seam.
“Visual and UT testing is required following each
weld, but we have alsonow introducesmagnetic particle
testing on some cans to ensure that we don’t miss any
surface cracks,” Jauka says, adding that each section
has flanges on its ends, “so the flange is the first and
last circumferential joint”.
At the top end of the growing line, completed tower
sections are lifted and placed on another set of 35 m
roller beds for testing. Following final inspection and
repair, a team of boiler makers is brought into the sec-
tion to mark off positions for internal bracketry and
fittings. Welders will then collect the relevant bracket
kit from stores and, using mostly flux-cored welding,
they weld them on.
The final operation on the fabrication side of the
line – the black section operation – is to do Easy-Laser
®
alignment and flame straightening on the flange sur-
faces. “Flange flatness must be within 2,0 mm across
the 4.5 m to 5,0 m diameter to ensure that when bolted
together onsite, the flanges seal against each other and
the bolts can be tightened without inducing stresses,”
Jauka explains. “The laser alignment system gives us a
printout highlighting twist and distortion, which is then
used to determine where flame straightening is needed
to bring the flange into tolerance,” he says.
From the top end of the line, the completed tower
section is brought back down the U-shaped facility on
a parallel path – the white section operation. It first en-
ters a wash bay for the removal of any gel, grits and oil.
Once dry, grit blasters are used to descale the surfaces
inside and out. For cathodic protection across the flange
connections of the tower sections, “we are required to
metallise an areawithin about 500mmof the flange and
all around access hatches and doorways with a 40
µ
m
layer of zinc. We therefore look for surface roughness of
between SA2 and SA3 fromour grit blasting operations,
before using the twin-wire arc spray process to deposit
the metallic layer,” he says. “Grit blasting also has to be
done under controlled humidity conditions, so we are
currently installing a humidity controller so that we will
no longer be dependent on appropriate ambient condi-
tions to complete this task.”
Following metalising, the tower section enters one
of three paint booths, PB1, PB2 or PB3. The section is
placed on a paint rotator supported and driven via the
flange rings on either side. This allows access to the full
surface for painting.
Once painted, the last stage of manufacture is to fit
the platforms, rails, ladders and internal fixtures onto
the welded bracketry. These components are also sup-
plied in kit form from Vestas. “We then move the tower
section into the yard for a final inspection. When we are
happy, we cover the ends attach the lower feet, enclose
the whole structure in tarpaulin and arrange for trans-
portation to site,” Jauka notes.
“It is currently taking us six to 10 days to complete
a top section, seven to 12 days for a middle section and up to 14
days for the bottom sections because of their heavier material
thicknesses. But we are not yet at full production. We hope to
be running all four lines in the near future, which will allow us to
complete six sections per week.
The facility was designed to produce 110 towers per year, or
330 sections. If we can persuade a few skilled people to join us
here in Port Elizabeth, we will soon be meeting our production
expectations,” he concludes.