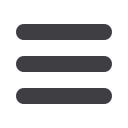

AFRICAN FUSION
March 2015
32
Robotic automation
A
ccording to the MD of a PE-based
catalytic converter manufactur-
ing facility, South Africans are
“na
ï
ve” about its capability. “We are
much more advanced than people
perceive,” he says, adding: “Within the
global group, this company is viewed
as a benchmark, not only for our capa-
bilities, we are also the go-to company
when there are problems in other parts
of the world. We export our talent, abili-
ties and locally developed solutions.”
In particular, this MD cites develop-
ments from its PE-based automation
and system integration partner, a com-
pany that, in association with Yaskawa
and the local catalytic converter indus-
try, is pioneering modularisation solu-
tions. “As far as robotic automation is
concerned, South Africa is up there with
the best of the world and this is clearly
evident from the export success of our
local automation partner, which is ex-
porting 12 modular integrated
handling andwelding cells from
PE inSouthAfrica toEurope,” he
tells
African Fusion
.
The design and manufacturing
complexity of catalytic converters “has
increased exponentially”, according
to Yaskawa’s Dale Palmer. The welds
and welding angles, weld penetration
profiles, fusion techniques and materi-
als are all more complex, which places
increasing pressure on manufacturers
to deliver a quality product without
jeopardising costs or productivity. To ac-
commodate this complexity, the robots
used in the catalytic converter industry
for handling and canning are now often
integrated into the welding cell.
“Vehicle manufacturers have very
stringent quality requirements: consis-
tent penetration; low levels of spatter;
smooth weld profiles; and very low
distortion and dimensional accuracy.
Also, while volumes are relatively high,
the mark-up allowed by catalytic con-
verter (CAT) manufacturers is next to
nothing. And as contracts are extended,
the prices per CAT paid to the manufac-
turer actually reduce,” reveals Palmer.
“The only way to meet these conflicting
requirements is to use expensive jigs to
hold the part duringmanufacture and to
do the welding using robots,” he adds.
“While the capital up-front costs might
be higher, once the system is running,
the unit costs drop quickly because you
can push volume through the system
without sacrificing quality.”
Describing how simple CATs for
vehicles aremanufactured, Palmer says
that catalytic converters have a ‘can’ as
the central component that contains
the expensive catalysing materials in a
honeycomb-structured element. “Typi-
cally, a cone is welded onto one side of
the can, then the part is turned around
for the opposite cone to be attached.
Then stud pipes with their flanges are
added. From an automation point of
view, there are several pieces being
joined, access is poor and assembly has
to be done progressively,” he explains.
At the heart of a typical welding cell
is a set of progressive jigsmounted onto
a Motoman RM2 rotating manipulator.
While welding is taking place inside the
cell, a completed part is removed from
the jig on the far right and each partly
assembled part is shifted one jig to the
right. New component pieces are added
and the empty jig on the left is filled.
On completion of each welding cycle,
the manipulator rotates, advancing
the process for each part by one step.”
Six distinct steps are performed by two
African Fusion
visits the Port Elizabeth robotics fa-
cilities of Yaskawa Southern Africa, takes a tour of
a local state-of-the art catalytic convertermanufac-
turing facility, and talks to Dale Palmer of Yaskawa
PE about the city’s vibrant automotive component
manufacturing sector and its increasing use of
robot-based automation.
Robot welding, catalytic converters and PE
SA’s benchmark city for robotic automation
At the heart of a typical welding cell is a set of progressive jigs mounted onto a Motoman RM2 rotating
manipulator.
Dale Palmer of Yaskawa PE.