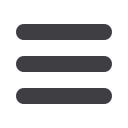

March 2015
AFRICAN FUSION
33
welding robots, effectively completing one part per rotation,
but advancing the assembly of five other parts by one step,”
Palmer explains.
In a further refinement to robot cells, he says that modern
CATs have an inner and an outer cone that are assembledwith
a fibre-mat between them, which acts as a heat shield. Prior to
welding, these parts are pressed together in an integrated ro-
bot cell, which accuratelymeasures part tolerances andmates
individual components to achieve the best possible fit. The
outer seams are thenwelded in the same cell, producing excel-
lent dimensional accuracies at exceptional production rates.
“In addition towelding, automatic conveying, measuring,
leak testing and quality certification are vitally important
aspects of the catalytic converter production process. We
therefore regularly team up with the systems’ integrators to
make the best use of robotic solutions. Robots are no longer
just a part of the welding system; they are now used for as-
sembly prior to welding as well as for the quality assurance
stages required after welding,” says Palmer.
The manufacture of larger converters for the truck and
bus industry, according to Palmer, has moved from Rosslyn
near Pretoria to Port Elizabeth. In one relocated plant, a jig-
less welding system is being used, where each welding robot
is ‘assisted’ by a handling robot. The jigless system relies on
a robot with a sophisticated gripper, which is used to pick up
a pre-assembled CAT, reposition it and then regrip it to make
sure it is heldaccurately in the reference position. The handling
robot then becomes a six-axis manipulator that allows every
seam to be accurately and optimally presented to the weld-
ing robot – and travel speeds and heat inputs are seamlessly
maintained regardless of path complexity.
“Following welding, the handling robot presents the
finished CAT to a checking fixture and, based on an accept/
reject decision, directs the component to the out line or the
repair line,” Palmer informs
African Fusion. “
This systemsaves a
fortune on jiggingwhen switching tomodified or newdesigns.
It also takes robotic welding to a whole new level of cost ef-
fectiveness and productivity. To do all of this using dedicated
automation and conveyorswould cost five timesmore and the
robots are much more easily synchronised,” he says, adding
that the process is “awesome to watch”.
For catalytic converters, almost all of the welding is done
using solid wire MIG welding processes, typically using 307
stainless steel consumables. “The SKS welding power source
is used as the standard for Motoman robot systems that we
supply, although many users would regard it as the ‘Rolls
Royce’ of welding systems. We know the SKS system’s quality
and reliability and we are able to offer an excellent back-up
service. We are available to help customers at any time – day
or night – to repair or replace a system and restore produc-
tion,” Palmer notes.
SKS power sources also offer a comprehensive range of
output options, including synergic sloping options, spatter
control and every type of pulsed waveform. “Different users
have their preferences but, generally speaking, the most im-
portant consideration is consistency. In this regard, the SKS
system includes a database that can record the parameters of
every completedweld. If there are any in-service quality come-
backs, it is possible to interrogate this database to determine
whether welding was performed according to the specified
procedure,” he assures.
While Yaskawa PE predominantly services the automotive
A view of Yaskawa PE’s demonstration, commissioning and repair facilities.
Testing of the critical dimensions of a catalytic converter weld for the
automotive industry.
industry, Palmer reveals that it is not all about welding. “Our
robots are used for hotmelt gluing operations to join the inner
and outer components of a motorcar headlight; we apply an
adhesive to the reflectors before the silver is applied; and a
clear coat is spray-painted onto the outer lenses. We are also
involved in welding wire seat springs; laser welding some of
the critical seat under frames; pouring foam into seat moulds;
and tending CNC lathes being used tomanufacture aluminium
shock absorber components.
“Any application that requires a repetitive task can be ro-
botised economically,” he continues. “In the pharmaceutical
industry, anti-retrovirals aremade inharsh environments from
dangerous chemicals. Instead of putting humans in harm’s
way to mix these chemicals, we use robots. It is safer and the
application becomes cleaner, more consistent and the end
product quality is higher.”
Packing and palletising applications are also becoming
more important. “We pack chlorine drums in the HTH factory,
for example, put chlorine bottles into boxes and then pack
boxes onto pallets,” he adds.
“In the past, robots were seen as complicated and ex-
pensive. This is no longer so. Today, a robot solution is a lot
cheaper than a CNC machine – and which workshop does not
have CNC machines?” Palmer asks.
“We are currently talking to a small fabricator looking
for a robot to meet its production needs. A robot might cost
around R360 000, and a decent welding system can cost from
R90 000 toR250 000, depending on the complexity required. So
a R500 000 investment can offer a reliable production system
that will run for 15 to 20 years, if maintained properly. Typical
payback periods are less than five years and robotsmake very
dependable employees,” he concludes.