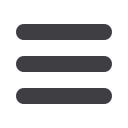

March 2015
AFRICAN FUSION
29
station until a green sticker is applied,”
he adds.
A plate with a green sticker then
proceeds to rolling: “Rolling is our critical
operation as it relies heavily on the skill
of the operator. We currently have two
roller operators rolling five to six cans per
shift, but we are operating our growing
lines on a pull-based production system,
so the rolling ratemust match the speed
of the of the whole line. We are looking
for at least two more plate rollers so
that we can implement a second shift,”
Jauka reveals.
To avoid double handling, the can
roller operator inserts some initial tacks
as soon as the required shape has been
established. Then a welder immediately
inserts a root run along the seam using
the solid wire GMAW process. The can
is then moved across to a submerged
arc welding station. The outside seam
is completed from the top. Then the can
is rotated by 180
°
and the remaining
welding is done fromthe insideat a lower
level. Immediately after welding, the can
is then re-rolled to correct any distortion
that may have been introduced.
“The crane operator then takes this
can and places it onto an orange block
painted on the floor. “As soon as a qual-
ity inspector sees a can on an orange
block, he does a visual inspection of the
welding and weld-bead profiles. Then
an ultrasonic (UT) inspection is done
on the seam – and this must pass. If any
flaw is detected, the inspector marks it
up and the can will be moved aside to a
separate repair station. Once repaired,
both magnetic particle (MT) and UT are
repeated until that can passes all tests.
“Once cleared by the inspector, the
can is moved onto the next available
greenblock. These greenblocks are used
to feed the growing line. Completed cans
are moved up towards Green Block 1,
which is the placeholder for the next can
required for the sectionbeing fabricated.
Our production target is tohave two cans
in the correct sequence ready to feed the
growing line at all times,” Jauka explains,
adding that, froma production perspec-
tive, “the idea is that a green block is
filled as soon as it become empty”. In
this way, the rate that cans are joined to
the tower sections will be matched to
the rate that cans are being produced.
On the growing line, ESAB roller beds
with built in manipulators are used to
support the growing section and the can
to be added. A set of hydraulically driven
transfer rollers lift the can clear of the
Rolling is the critical operation as it relies heavily on the skill of the operator. DCD Wind Towers
currently has two roller operators rolling five to six cans per shift.
Following rolling, the outside seam is completed from the top. Then the can is rotated by
180° and the remaining welding is done from the inside at a lower level.