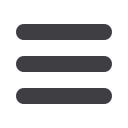

March 2015
AFRICAN FUSION
25
Testing according towelding standards EN288-2,3was car-
ried out. Mechanical properties, microstructure and results of
fractographic analyses were used for assessment of individual
weldments. Mechanical properties satisfied requirements.
Special attentionwas paid to critical zones of weld joints from
a point of view of crack propagation.
Microstructural analyses of individual weldments were
carried out using light (LM), scanning (SEM) and transmission
electron microscopy (TEM) in a range that was necessary for
optimisation of the production process. Crossweld hardness
profiles of individual weld joints were compared with results
of microstructural analyses. Hardness wasmeasured near the
face of eachweld joint, in the centre and across the root. Hard-
ness profiles in the Figures shown are all taken at the central
parts of weldments.
Results
Similar weld joint A
The base material of 27NiCrMoV 15-6 steel underwent special
heat treatment in order to obtain mechanical properties near
those of the weld metal. The temperature of final annealing
was as high as possible, but lower than that which could
cause recrystallisation with an associated undesirable drop
in strength properties. The appropriate temperature was
selected on the basis of mechanical properties and detailed
microstructural analysis using TEM.
The microstructure of the base material condition before
welding corresponded to a tempered mixture of bainite and
martensite. Relatively coarse particles of cementite and finer
Cr
7
C
3
carbides were observed in bainitic regions (Figure 2a)
while only very thin precipitates occurred in tempered
martensitic laths. A higher dislocationdensitywas characteris-
tic formartensite (Figure 2b). If the annealing temperaturewas
kept high, then small crystallised grains appeared (Figure 3).
The goal of TEM analysis was to find an optimal annealing
temperature in order to avoid recrystallisation.
The crossweld hardness profile after optimised heat
treatment is shown in Figure 4. Hardness of the weld metal
was lower (from 230 to 241 HV10) than that of the base ma-
terial (from 270 to 285 HV10). The local maxima in the heat
affected zones near the fusion line did not exceed the value
of 314 HV10. In compliance with the hardness profile, tensile
tests ruptured in the weld metal, even though the desired
Figure 1: Macrostructures of trial weld joints.
Figure 2: TEM micrographs of Weld A base material: a) bainitic
structure, b) bainite with tempered martensite in the central parts.
Figure 3: TEM micrograph of Weld A showing small recrystallised
grains.
Figure 4: The crossweld hardness profile of Weld A after PWHT.