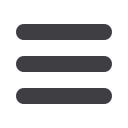

March 2015
AFRICAN FUSION
No Orient Flaw Type
Flaw Size(inch)
Length Depth % Depth
1
Circ.
Crack
0.30
0.085
55
2
Circ.
VLOF
0.40
0.085
55
3
Circ.
Crack
0.42
0.035
22
4
Circ.
HLOF
0.36
0.102
66
5
Circ.
Crack
0.71
0.050
32
6
Circ.
Crack
0.48
0.032
20
Parameter
Setting
Gain
37 dB
Digitising frequency
50 MHz
Inspection mode
Pulse-echo
Steering angle
35°to 80°
Angle resolution
1.0°
Voltage
80 V
mens and six flaws in total were inserted into the specimens.
Types of inserted flaws include a fatigue crack developed
from the triple point, horizontal lack of fusion (HLOF), which
occurs at the boundary of the piping and the weld metal, and
vertical lack of fusion (VLOF), which occurs at the boundary
of the coupling and the weld metal. Detailed specifications of
the flaws inserted are provided in Table 2.
Experiment apparatus
The ultrasonic probe was manufactured based on design
parameters verified through the modelling. Figure 5 displays
the shear wave phased array ultrasonic probe manufactured
in this study.
For the phase array ultrasonic instrument, ZETEC’s Omnis-
can, which has 16 channel operation capability and is portable
for site inspection, was used. The signal obtained from the
Omniscanwas connected via TCP/IP communication protocol
for storage on a laptop computer, andUltravison version 1.1Q6
was usedas the signal evaluation software. For the experiment,
the apparatus was set up as shown in Figure 6.
For the experiment, a scanner was clamped to the flawed
specimens and then a base point was determined. Subse-
quently, the scanner revolved 360
°
in the circumferential
direction around the specimens and captured the signal. The
setting values of the phased array ultrasonic test instrument
used for the experiment are seen in Table 3. After entering the
setting values for operation of the probe, the ultrasonic beam
was generated at angles ranging from 35
°
to 80
°
.
Results and review
The experiment was carried out using the flawed socket weld
specimens with a fatigue crack and lack of fusion (LOF) flaws.
Based on the results, the signal was evaluated. For the fatigue
crack specimen, as the coupler welded onto the piping was
elbow-shaped and manufactured from a casting, inspection
of the coupler was not possible. The scanner was therefore
clamped to part of the piping before obtaining the signal.
Figure 7 illustrates the results of the inspection using a
flawed specimen with a nominal diameter of 1.0″ and a leg
length of 1:1. As seen in the figure, three flaws including the
LOF and a fatigue crack were detected at the front and a rear
angle of 46.5
°
– within the range of refraction angles from
35
°
to 80
°
– and the length of the flaws was measured at the
signal of the B-scan. As a result of measuring the length of the
specimen with a leg length of 1:1, the length of the fatigue
crack and LOF flaws were measured to be slightly longer than
the actual length. As the crack tip signal was not confirmed at
the obtained signal, it was not possible tomeasure the depth.
TheNo. 3 crack flawapplied to the specimenswas a fatigue
crackoriginatingfromthetriplepointandevolvedintotheinter-
nal diameter of the piping. As the crack grew in the same direc-
tionas theultrasonicwaveheaded toward it and tiltedat a large
angle, a relatively small amplitude was identified for the flaw.
Figure 8 shows the results of an experiment for a flawed speci-
men with a leg length of 1:2 . As seen in the figure, one LOF
flaw and two fatigue cracks were detected and the length of
the flaws was measured from the B-scan signal.
In the case of a flawed specimenwitha leg lengthof 1:2, the
No. 5 crack and No. 4 HLOF flaw were found to have a higher
level of amplitudewhile aNo. 6 crack flawwith 20%depthwas
found to have a low level of amplitude. A size evaluation of the
six flaws included in the flawspecimens is presented inTable 4.
Table 2: Detailed information of the flaws contained in flawed specimens.
Figure 5: The shear wave phased array ultrasonic probe for small
bore piping socket weld.
Table 3: Experimental parameters.
Figure 6: Experimental setup of phased array ultrasonic system.
21