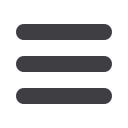

23
March 2015 AFRICAN FUSIONFigure 7: Signal evaluation results of flawed specimen with leg
length of 1:1.
Figure 8: Signal evaluation results of flawed specimen with leg
length of 1:2.
No Type
Actual
Measured Deviation
#1 Crack
0.30
0.35
-0.05
#2
VLOF
0.40
0.47
-0.07
#3 Crack
0.42
0.43
-0.01
#4 HLOF
0.36
0.35
0.01
#5 Crack
0.71
0.59
0.12
#6 Crack
0.48
0.47
0.01
Table 4: Flaw sizing results for specimen.
Conclusion
For phased array ultrasonic testing designed for inspecting
piping welds in a nuclear power plant or industrial structure,
a 3.5 MHz shear wave phased array ultrasonic probe was
designed and developed with 16 linear type piezoelectric
elements capable of generating an ultrasonic beam at angles
ranging from 35
°
to 80
°
in order to inspect small bore piping
socket welds without using a wedge for high accessibility.
With the aim of analysing inspection results off-line in
variousmodes, a semi-automatic scanner was developed. The
scanner enabled the phased array ultrasonic probe to encode
its location while revolving in the circumferential direction
and maintaining contact on the small bore piping. Using the
developed shear wave phased array probe and a manual en-
coder scanner, anexperiment involving specimenswith fatigue
cracks was carried out to detect six different flaws.
In conclusion, application of the inspection system de-
veloped in this study to the small bore piping socket weld of
a nuclear power plant is expected to reduce the inspection
time. This will not only contribute to reducing the inspector’s
exposure to radiation but also to improving the reliability of
socket weld inspection.