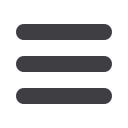

AFRICAN FUSION
March 2015
28
Wind tower fabrication
T
rainedat theNelsonMandelaMet-
ropolitan University (NMMU) in
Port Elizabeth, Jauka joined DCD
Wind Towers in November 2013 at the
starting point of commercial production.
“I did a degree in industrial engineering
and, after working at a local Goodyear
facility for a few years, I joined DCD to
improve the production efficiency of the
wind tower fabrication process. To re-
main competitive, we need to find ways
to cut away non value adding operations
and to promote those activities that are
directly incorporated into theprice of our
product,” he tells
African Fusion.
“The core value adding activity of
this facility is welding, and we employ
mainlyGMAW, FCAWandsemi-automatic
submerged arc welding,” Jauka contin-
ues. “But my experience is production,
so I am learning about welding all the
time,” he adds.
Describing the particular require-
ments for wind tower manufacturing,
he says that the key productivity goal is
to balance each part of the production
line so that the fabrication of each wind
tower segment proceeds steadily and
efficiently through the plant, without
causing delays or inactivity further into
the process.
The plate for the first commercial
can was cut on Saturday February 15,
2014, for a Vestas V112, 3,075 kW wind
turbine destined for InnoWind’s Grass
Ridge project 25 km South of PE. DCD
Wind Towers has now completed and
delivered five three-section towers for
this project, which was commissioned
during January this year. In total, this
plant has 20 turbines capable of produc-
ing 61.5 MW which, at a capacity factor
of 25%, is equivalent to 134.7 GWh of
power per year – enough to supply the
basic annual needs of up to 40 000 South
African households.
“Our current work also involves
Vestas turbines for a secondwindproject
dubbed ‘Chaba’.” The requirement is
for seven towers split into 21 separate
sections, which will support turbines
supplying 21 MW of power to the Great
Kei municipality at Komga, up near the
Kei River north of East London. The
first turbine is due to be operational in
July 2015, with the facility reaching full
capacity in September. For this project,
DCD Wind Towers will locally build all of
the wind towers.
DCD’s fabrication process, accord-
ing to Jauka involves fabricating three
structural section for each tower, a top
section, a middle section and a base
section. Each of these is flanged so that
the 84 mtowers can be erected onsite by
bolting them together. Each individual
section is made by welding together a
series of cans, which vary in diameter
and plate thickness – 5.0 m in diameter
and 38mm for a typical base section and
3,5 to 4,0mand 16mm thickness for top
sections. “Each section consists of 9, 10
to 11 cans, most of which are tapered,
so fabrication has to be done in a strict
sequence,” he explains.
Four growing lines
The concept being employed to achieve
production and cost efficiency is ‘grow’
each tower section, can by can, on a
growing line. “We have four parallel
growing lines at this facility, which all
need to be busy and balanced for maxi-
mum output capacity and efficiency,”
says Jauka. “For each line, the idea is
that we cut, roll and seal a can, then we
join that can to the previously completed
one. So we join and grow, join and grow
until the tower is the required length.
Thenwe add the end flange. But balanc-
ing the work on the growing lines is also
important. Fabricating bottomsections,
for example, takes up 45% of the total
welding time, because of the thicker
section plate being welded particularly
on the threebottomsectionswith38mm
plate thicknesses,” he tells
AfricanFusion.
“At any one time in the plant, we aim
tohave one canbeing joined to the tower
section in one of the lines, a can-to can-
fit-up being completed on the second
line, can rolling on the third line and
plate cutting for the fourth,” he notes.
At the fabrication starting point a
plate is put through a wheel abrator to
take off the rough scale. “The abrator
blasts grit onto both sides of plate as it
enters the facility. From there, a three
headed CNC-controlled ESAB oxyfuel
cutting system cuts the plate to size,
while simultaneously bevelling the
edges for welding. Due to the different
conical shapes of each can in a segment,
each sequential can has a different size,
so automatic control of this process
is essential and each can has its own
unique identifier that is generated be-
fore the plate enters the facility,” Jauka
explains.
The cut plate is then taken toa cham-
fering table to polish and clean the bevel
and take off the dross. “At this stage we
have our first quality hold point. The
quality controller checks that the plate
is dimensionally accurate for the specific
can and tower section being fabricated,
to within around 1.0 mm of tolerance.
If okay, he places a green sticker on it,
but the plate will remain at the holding
DCD Wind Towers was set up in March 2013 and be-
gan producing tower sections later that year.
African
Fusion
visits the company’s fabrication facilities in
the Coega industrial development zone (IDZ) and
talks to productionmanager, Leonard Jauka, about
its processes and capabilities.
Wind Tower fabrication:
the DCD way
Wind Towers’ production manager, Leonard Jauka.