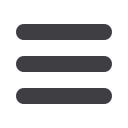

AFRICAN FUSION
March 2015
38
Welding and cutting
The torch: the focus for automation
A
utomotive supplier Johnson Con-
trols in Lahnwerk (JCI), Germany,
has managed to eliminate a bottleneck
in welding processes for joints in car
seat structures. The welding experts at
the production site in Dautphetal are
now using SKS’ Power Clutch torch sys-
tem for components such as SGR tubes
and brackets. Viktor Werz of manu-
facturing engineering at JCI confirms:
“After switching to welding systems
with SKS torches, the seams now meet
our quality standards at higher welding
speeds and with shorter cycle times.”
At the facility, JCI manufactures
high-quality car seat structures using
S420 MC tubes and have found a smart
way to combine high-tech electronics
and mechanical creativity. SGR tubes
and bracket parts are joined by feeding
the diagonally cut end of a 38 mm tube
through a round extended and beaded
hole in a 3.0
mm
-thick metal pressing,
and thenwelded around a circular seam.
Tomove along the seam, thewelding
robot needs a reference point to start
from and any positional deviation must
be identified and compensated for. Con-
ventional techniques for determining
this point involved errors and additional
costs after each change of a gas nozzle.
Torches also become distorted by heat
and require continuous realignment.
The solution from SKS Welding
Systems eliminates these shortcomings
by dealing with the cause: an annular
circumferential ridge on the retaining
headof the torchnowdefines a reference
position that is independent of the gas
nozzle. The ‘workpiece search’ function
uses this ridge. A test voltage is applied
to the retaining head. Upon contact with
the ridge, the robot controller receives a
correspondingmessage and calculates a
robot path that is adapted to the specific
position of the workpiece.
The high TCP (tool centre point)
accuracy of the torch is, therefore,
maintained between each changover.
“We now achieve extended tool life and
higher welding speeds. Cycle time has
been reduced by twelve seconds per
part,” says Werz.
www.yaskawa.za.comUnique Welding Alloys relocates
U
nique Welding Alloys’ Boksburg
branch has outgrown its Cason
Road premises, and has relocated
to bigger premises at the company’s
distribution centre on 19 Van Dyk road.
“We saw this as an ideal opportunity
to rationalise operational costs in order
to continue tooffer competitively priced,
quality products to our customers,” says
managing director, John Smithyman.
“Our customers will also experience
improved turnaround time due to a new
gas ramp and ample, secure parking,” he
adds. The new premises also have an
onsite service centre, ensuring awin-win
for both Unique Welding Alloys and its
customers.
The holding company, Weldamax,
recently merged all its divisions: Wel-
damax, Unique, Selrod and Maxweld
andBraze intoone tradingentity, namely
Unique Welding Alloys, and the reloca-
tionand rebranding of the newBoksburg
branch is in line with phase one of this
merger.
www.weldamax.co.zaWire feeders with all-round protection
F
ronius has expanded its Case
wirefeeder range for mobile use in
harsh environments. In addition to the
VR 5000 Case that has been available for
the TransSteel power sources for quite
some time, the company has now intro-
duced suitable wirefeeders for the TPS/i
(WF 25i Case) and TPS (VR 4000 Case)
series. Users can choose between
versions with a standard spool
(D300) or a small spool (D200).
The completely closed and
shock-resistant devices are pro-
tected against dust, humidity
and water spray, making them
particularly suitable for use on
oilrigs, in shipbuilding, for rolling
stock manufacture and anywhere
where harsh environmental condi-
tions prevail.
www.fronius.comDeveloping young
welding talent
A
ir Products South Africa’s Josua
Le Roux, GM central support
says: “Welding skills are critical in
many industries and it is no secret
that there is a dire shortage of engi-
neering skills worldwide, specifically
when it comes to expert welding.
It is, therefore, our great pleasure
to have provided welding gases to
facilitate the Young Welder of the
Year competition at the SAIW.”
Air Products provided various
specialist gases including argon for
TIG welding and its special blends:
Coogar 82 for MIG welding and
Fluxblend for flux-cored welding. In
addition, the company contributed
towards accommodation and other
costs related to the competition.
“We are passionate about train-
ing, skills development and the
empowerment of young people in
South Africa,” says Le Roux. “It is our
hope that the use of Air Products’
range of specialist welding gases and
the experience in taking part in this
event will have an extremely positive
impact on the future careers of these
young welders,” he adds.
www.airproducts.co.zaThe flanged seam that leaves a small
section free for a ‘nose’ in the notch of the
metal pressing.
Fronius’ VR 5000 Case wirefeeder for D300 spools is
protected against dust, humidity and water spray.