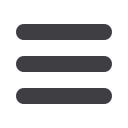

The modern pulse waveform optimisation and control algorithms
embedded in Weco’s HSL machines, while based on the well established
synergic concepts of one-droplet per pulse, result in a more focussed
(stiffer) arc, higher welding speeds and better penetration. “The HSL range
offers up to 40% increases in welding speed because the system is able to
maintain a very stable arc with a shorter arc length and longer stick-out.
The net result, since heat input is inversely proportional to travel speed, is
lower heat input,” Toniolo explains.
Underpinning the added stability and stiffness of the short welding arc
is the very rapid and well controlled response times to naturally occurring
arc events, such as short circuiting, along with thorough optimisation of
synergic pulse wave welding characteristics and wire feed speed combi-
nations for each material, consumable size and gas combination. “This,
alone, involved a two year development programme by a teamof excellent
welders,” he adds.
“We have also worked very hard to enable welders to understand
the machine. Sometimes modern technology can only be understood by
engineers, but it is welders who use the machines on a daily basis, so they
need to know the machines intimately. We have developed a machine for
practical people that can be set up and used quickly, without unnecessary
complications,” Toniolo assures. While parameters can be locked into the
machine, the welder can always adjust the arc within some limits. “But we
can also leave the machine open. We believe it is simple enough to leave
an experienced welder in total control,” he adds.
According to the marketing brochure, Weco’s Pulse HSL power source
offers: speed on average 35% better that standard pulse equivalents; de-
position rate increases of up of 15%; deeper penetration and lower risk of
lack of fusion; reduce heat input, by a corresponding 35%; alongwithbetter
welding quality and mechanical/metallurgical properties. The system is
shown on a video completing a 10 mm fillet weld at speeds improving from
13.8 to 19.7m/min. “And the lower heat input results in less distortion and
a smaller HAZ. This has a hugemetallurgical advantage because it reduces
HAZ hardness and improves toughness,” Toniolo points out.
Also shown on the video is the double pulse feature being used toweld
aluminium. “Double pulse is mostly for aesthetics. The synergic features
of this machine allows us to superimpose a low frequency pulse over the
higher metal transfer pulse frequency. This gives a weld bead similar to a
pulsed TIG weld, with a waved surface profile.
“Also, though, for positional welding, the low frequency pulse allows
the welder to better control the weld pool. If welding vertical up, for
example, weaving becomes unnecessary. The welder simply moves up
during a low pulse, while the new weld pool below cools down. Double
pulsing also helps the welder to pace the weld. Just as a metronome
helps to keep musicians in time, double pulsing helps the welder to pace
welding for a more consistent bead profile and a high quality aesthetic
finish,” Toniolo suggests.
“In South Africa at the moment, we are focusing on manual machines
that help welders to produce better quality,” continues Amaral. “We are
striving to introduce these technologies slowly and in the right way. So
our first priority is to introduce machines for operators. We will, of course,
also be introducing robot machines when the need arise, which we know
will offer additional productivity advantages.”
He says that welding is a sensitive business and “without a support
offering, the business can’t be sustained. Our strategy is not simply to offer
the Smarter andWeco brands ofmachines. Like a tailor, we have developed
solution packages for the Africanmarket. We train people to weld with the
machines and to repair them. We install test facilities to suit our equipment
and to help to calibrate them – and we guarantee to respond to amachine
issue within 24 hours and to resolve it within 72 hours.
“For theWeco and Smarter brands in South Africa, themachine quality
and service standards offered will be the same as those taken for granted
across Europe,” Amaral concludes.
Launched at an open day in February at the company’s
Meadowdale premises in Gauteng, South Africa, Weco’s Power
Pulse HSL (high speed line) being set up by Pierre van Heerden
(left), Smarter Welding Africa’s welding specialist.
Jens Steinbach fromWeco Europe demonstrates HSL in double
pulse mode on a vertical up aluminium fillet weld. Mostly for
aesthetics, double pulse gives a weld bead similar to a pulsed
TIG weld. It also helps welders to better control the fluidity of
the weld pool.
March 2015
AFRICAN FUSION
37