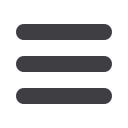

AFRICAN FUSION
March 2015
40
INDEX TO
ADVERTISERS
Afrox ......................................................................8
Air Liquide...........................................................20
Air Products ........................................................23
BED Holdings: Fronius........................................10
Crown Publications.......................................... IBC
ESAB....................................................................22
Lincoln Electric.......................................OFC, OBC
Probraze Metals..................................................15
Renttech .............................................................14
SAIW ......................................................................2
SKS Welding Systems.........................................13
Smarter Welding Africa .....................................IFC
voestalpine Böhler Welding SA..........................34
Yaskawa Motoman SA ........................................30
Today’s technology
Refurbishment using the PTA process
Journals and pot roll scraper blades for the zinc
galvanising process, for example, are coated with a
cobalt-based layer for high temperature wear and
corrosion resistance.
T
he plasma transferred arc (PTA)
welding and hardfacing process
from thermal spray and surface en-
gineering coating specialist, Ther-
maspray, provides a versatilemethod of
depositing high quality, metallurgically
fused deposits on relatively low-cost
substrates.
First introduced in 1964 to better
control lower current arc welding, the
PTA process is complimentary to both
thermal spray and conventional weld-
ing and is mainly used on components
that are subjected to severe corrosion or
abrasion, thermal shock, slurry erosion
or extreme impact forces. The process
offers the necessary protection to the
substratebyproviding a coating that can
withstand these conditions. PTA can be
applied in practically every case where
hardfacing is needed.
According to Shaik Hoosain, metal-
lurgical engineer at Thermaspray, a
wide variety of materials, ranging from
soft to medium hardness (e.g., stain-
less steel) to very hard, wear resistant
materials (e.g., carbide composites), can
be deposited using the PTA process to
achieve diverse surface properties such
asmechanical strength, wear, corrosion
and creep resistance. Bead thicknesses
range from1.2 to 2.5 mmandmulti-pass
runs depend on the application.
Hoosain explains that the plasma
arc welding process uses a plasma to
transfer an electric arc to theworkpiece,
a process which he says is similar to gas
tungsten arcwelding (GTAW). “To create
plasma, a gas, typically argon, is heated
to a sufficiently high temperature and
ionised so that it becomes electrically
conductive. The plasma welding torch
contains a negatively charged non-
consumable tungsten electrode within
a positively charged copper nozzle with
a small orifice at the tip,” continues
Hoosain.
“A pilot arc is struck between the
torch electrode and the nozzle tip and
the arc is transferred to the metal to
be welded. By constricting the plasma
gas and the arc through the orifice, the
torch delivers a high concentration of
heat to a small area, which leads to high
quality welds.” For hardfacing, an alloy
powder froma hopper is introduced, via
a carrier gas, into the plasma stream.
This forms a fused layer on the surface
being coated, with the required alloy
properties.
The plasma transferred arc process
offers a number of important advan-
tages over conventional arc welding,
including:
•
It is easily automated and offers a
high degree of reproducibility.
•
Precisemetering ofmetallic powder
feedstock allows lessmaterial to be
used compared to traditional weld-
ing processes.
•
Precise control of the welding pa-
rameters also offers a high degree
of consistency.
•
Controlled heat input, less than
conventional arcweldingprocesses,
ensures weld dilution can be con-
trolled to between 5.0 and 7.0 %.
•
The deposit of a specific alloy
is tougher and more corrosion
resistant than those producedusing
GTAW or oxy-fuel processes.
•
PTA weld deposits have character-
istically less oxides, inclusions and
discontinuities.
•
Post weld machining is minimised
due to the smooth deposit created
through the PTA process.
Typical PTAapplications successfully un-
dertakenby Thermaspray include the re-
furbishment of the process rolls used in
the steel industry. Journals and pot roll
scraper blades for the zinc galvanising
process, for example, are coated with a
cobalt-based layer for high temperature
wear and corrosion resistance. “Scraper
rings formanufacturing gearbox compo-
nents are also PTA-coated with cobalt-
base alloys, as are valve seats used for
high temperature steam valve compo-
nents. And components used in glass
manufacturing are PTA-coated with a
nickel-basedalloy toprovide impact and
wear resistance at high temperatures,”
adds Hoosain.
In closing, Hoosain says that be-
cause the PTA welding process has
not received as much attention in
South Africa as conventional arc weld-
ing processes such as GTAW, it is an
under-utilised welding process in the
local market. “PTA is a versatile, high
temperature, wear and impact resistant
welding process that is ideally suited to
a wide range of applications, ensuring
highqualitywelddepositswith excellent
reproducibility frombatch to batch. It is
ideal for severe impact, wear and cor-
rosive environments.”
In addition to PTA welding, Ther-
maspray also provides a comprehensive
range of support coating finishing tech-
nologies including machining, grinding
and burnishing from its state-of-the
art facilities in Olifantsfontein, Johan-
nesburg.
www.thermaspray.co.za