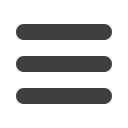

34
MODERN QUARRYING
October - November 2016
SUPPLIER
SPOTLIGHT
D
elivering high quality bulk
emulsion to a remote island
in the Atlantic Ocean – and
ensuring problem-free
blasting for a two-year proj-
ect – has proved BME’s ability to design
and manufacture a safe and reliable
product suited to the most demanding
conditions.
“Supplying and blasting over 4 000 t
of HEF emulsion for the building of the air-
port on St Helena island was a demanding
task for a number of reasons,” says Albie
Visser, BME’s general manager for South
Africa. “But the experience showed what
could be achieved by our commitment to
innovation and quality.”
Situated over 2 200 km from the
Namibian harbour town of Walvis Bay,
This issue’s Spotlight goes to BME, a company that is a leading
supplier of explosives and services to the African mining, quarrying
and construction industries. Focusing on safety, supply security
and value-adding technical services, the company supplied and
blasted over 4 000 t of HEF emulsion on St Helena Bay island,
and is currently tackling nitrate mine water contamination –
addressing the issue of water quality and conservation.
BME evolves
its technology to new levels
St Helena is one of the world’s smallest
inhabited islands – measuring only 8,0
km by 16 km and inhabited by just 5 000
residents. In a step towards making the
island more economically self-sufficient,
the British government announced in
2005 that an airport would be built on the
island – which traditionally could only be
reached by the mailship
RMS Saint Helena
.
The construction of the airport was an
ambitious plan that would require sub-
stantial blasting and earthmoving, involv-
ing 8-million m
3
of material in a dry-cut fill
operation.
“BME had to design an emulsion so
stable that it would withstand the long
sea voyage, in addition to the road trip
of 1 700 km to Walvis Bay,” says Visser.
“It would also have to endure multiple
re-pump events, and widely varying ambi-
ent temperatures between 3,0 degrees
and 34 degrees.”
Most emulsions tend to become
thicker the longer they stand or the colder
the surrounding temperature; variations
in temperature can also lead emulsion
to break down. However, manufacturing
the product on site in St Helena proved
unviable due to the lack of infrastructure
and insufficient energy supply; hence the
Delivering high quality bulk emulsion to a
remote island in the Atlantic Ocean – and
ensuring problem-free blasting for a two-year
project – has proved BME’s ability to design
and manufacture a safe and reliable product
suited to the most demanding conditions.
BME operations manager Neil Alberts.