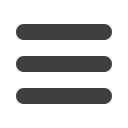

October - November 2016
MODERN QUARRYING
35
When we are kids we like to play with toy trucks… BELAZ Africa: we provide big trucks for big mining! www.mynbou.com … when kids grow so do the trucks … … and we cannot stop admiring these giantsSUPPLIER
SPOTLIGHT
decision to locally manufacture a product of remarkable resilience,
and transport it in its emulsion state.
“We went the extra mile to ensure that all the materials were of
the best possible quality, including the used oil, so that the emul-
sion remained fluid throughout its six-month life-cycle, frommanu-
facturing in South Africa through to blasting on St Helena,” he says.
“This meant extending our already stringent quality standards, and
applying them to every tonne of the approximately 4 000 t of HEF
that the project required.”
From the factory in Fochville, BME transported the emulsion
by tanker to its silos near Swakopmund in Namibia, and then into
ISO-containers (isotainers) for loading onto the ship bound for St
Helena. To deal with the steep gradients up to the work site on
the island, emulsion was pumped from the isotainers into a con-
verted water bowser before transportation to site – where it was
re-pumped back into the isotainers.
“With this number of pumping events, the potential for emul-
sion breakdown becomes significant,”Visser explains,“but our prod-
uct maintained its integrity even beyond our target levels. In fact,
looking at howwell the product withstood these conditions, we can
confidently say that it would still be usable after a year.”
The first BME truck was on site and ready to go in October 2012,
and in November the first blast – consuming 74 t of bulk explosive
– was detonated on St Helena.
“Over the roughly two-year period from November 2012 to
August 2014, the operation consumed about 200 t of HEF 100 emul-
sion a month,” he confirms. “We supplied the contractor with up to
18 blasts per month, totalling some 54 000 holes in total; each hole
was 89 mm in diameter and averaged 12 m deep.”
According to Visser, the key to a good emulsification process is
the right surface active agent (or surfactant) – the emulsifier. “Our
in-house experts developed the emulsifier specifically for the St
Helena project, in the same way that we develop emulsifiers to suit
the raw materials in whichever environment we operate.”
He emphasises BME’s use of a dual oxidiser – or ‘double-salt’ –
system, which gives more stability to the product than a single-salt
solution.“We were pleased that our emulsion had the long shelf-life
that we required and was extremely tolerant to multiple pumping
cycles – proving highly resistant to breakdown even under exces-
sively stressful conditions.”
This was achieved through a demanding regime of testing over
a number of months leading up to the project’s commencement –
using elevated temperatures, for instance, to accelerate the ageing
of the products and to ensure it could last the long periods on the
road, at sea and standing on the island awaiting use.
“Our product standards ensured that every tonne manufac-
tured was the same high quality – whether it was made the next
day or the next year,”he says.“We made sure there was no variability
in the quality.”
BME pioneered the use of cold emulsion explosive in South
Africa over 30 years ago, and is today a market leader in blasting
solutions for the mining, quarrying and civil engineering sectors.
Tackling nitrate contamination
In South Africa’s increasingly water-scarce and environmental-
ly-regulated mining industry, BME’s emulsion explosives help
keep nitrates out of mine water, preventing possible groundwater