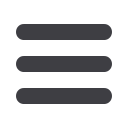

Hypertherm’s Centricut brand engineers
and manufactures advanced plasma
and laser cutting consumables. Its
product line includes consumables that
can deliver increased value to users of
most cutting systems, including systems
from ESAB, Kjellberg, and Trumpf.
All Centricut products are engineered
and manufactured to exacting standards
and incorporate the latest technological
advances that help to reduce operating
costs, while delivering increased cut
speed and quality.
The company has launched new
technology to benefit owners of
Kjellberg
®
plasma cutting systems.
Operators of Kjellberg’s FineFocus
800 and 900, as well as its PA-S70
and PA-S75 products, can now
purchase nozzles that are claimed to
last twice as long as current Kjellberg
nozzles. The nozzle life is increased,
and operating costs reduced, through
the use of patent pending CoolFlow
™
technology and patented SilverLine
®
technology.
Centricut’s CoolFlow technology was
developed using advanced modelling
software that enabled engineers to
closely study heat distribution within the
nozzle, as well as the cooling process.
Centricut engineers then worked to
Increased nozzle life
for plasma cutting systems
Stainless steel and
nickel alloy tubes
design a nozzle that would funnel the
cooling fluid to the hottest areas of the
nozzle. The end result is money saved
for customers, because the nozzle stays
cooler and lasts longer.
The CoolFlow technology is combined
with Centricut’s patented SilverLine
electrode technology to further
increase nozzle life. To create SilverLine
electrodes, Centricut’s machinists use
a combination of silver and copper to
increase electrode life.
“The increased life span of the CoolFlow
nozzles will help Kjellberg owners save
money, since advanced Centricut
technology translates into a need for
fewer consumables,”
commented Dean
Lizotte, team leader for Hypertherm’s
Centricut brand.
Hypertherm designs and manufactures
advanced plasma cutting systems for
use in a variety of industries, such
as shipbuilding, manufacturing, and
automotive repair. Its product line
includes handheld and mechanised
plasma systems and consumables,
as well as CNC motion and height
controls.
Hypertherm
– The Netherlands
hteurope.info@hypertherm.com www.hypertherm.com/euFounded in 1974, Italian company
Tecnofar SpA is a specialist in the
manufacture of stainless and nickel
alloy tubes. With advanced technology,
the company has two production units,
located inDelebioandGordona, covering
a total surface area of 7,000m
2
.
The company produces redrawn
precision tubes, both in bar and coil
form, using the TIG welding process.
The company offers a modern, well-
equipped department for tube cutting
and is able to produce cut pieces
measuring just a few millimetres in
length, completely burr-free.
Tecnofar can adhere to a range of
dimensional tolerances, with a stainless
steel tube range of 0.3 to 76mm and
wall thickness from 0.1 to 3.5mm. These
tubes are produced using stainless
steels provided and guaranteed by
leading steel mills.
ISO 9001:2000 accredited by Italcert,
the company has been certified by
RINA for its welding system and heat
treatment for the production range of
OD 6-19mm and wall thickness of 0.4
to 1.1mm.
Tecnofar spa
– Italy
info@tecnofar.it www.tecnofar.itdevelopments
products &
Photo – TS Steel Pipe & Fittings Srl – see page 20
18
Tube ProducTs InTernaTIonal January 2009
www.read-tpi.com