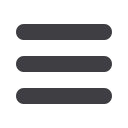

60
Wire & Cable ASIA – January/February 2014
www.read-wca.comTo ensure high productivity of the stringing process a good
quality, straight, soft and properly soldered ribbon has
to be used. Accurate laying of the PV ribbon also has to
be ensured during the stringing, tabbing process. Good
quality interconnect ribbon will inevitably reduce stringer
downtime and its scrap rate. Today’s high-speed stringers
require ever more demanding ribbon specifications.
The three key trends in PV ribbon specifications include:
• Ever tighter tolerances of solder thickness and ribbon
straightness are driven by new generation fully
automated, high-output stringers
• Lower ribbon yield strengths (Rp0.2%) are required for
increasingly thin solar cells
• New panel designs utilise three interconnect ribbons
per cell instead of two, reflected in a growing demand
for smaller (narrower and thicker) ribbons. This in turn
drives capacity expansion of precision tinning lines for
small interconnect ribbons
PV ribbon specifications
and requirements
The conductor or base material in the PV ribbon is
high-conductivity, high-purity copper. Copper used in PV
ribbons is typically ETP, DIP form copper or oxygen-free
copper (OFC: CD-110, CD-101, CD-102).
Copper wire is rolled in a rolling mill to produce copper
ribbons, which are subsequently tinned/soldered in a
tinning line to produce PV ribbon. Some producers use
an alternative process of copper strip slitting to produce
copper ribbons, which are generally of lower quality.
The size range of bare copper ribbons (inlet material for
tinning line) is as follows:
• PV bus bar: width [3mm-6mm] x thickness
[0.2mm-0.5mm]
• Interconnect ribbon: width [1mm-3mm] x thickness
[0.08mm-0.2mm]
Copper ribbon tolerances vary among producers. They
depend mainly on the type of rolling mills deployed,
the quality of input material and the know-how of the
manufacturer. Typical tolerances for producers with good
rolling capabilities are:
• Width tolerance: ±8 micron-±15 micron
• Thickness tolerance: ±8 micron-±13 micron
The mechanical properties of PV ribbon that are commonly
sought by panel manufacturers are:
• Tensile strength: <250 MPa
• Elongation: >20%
• Camber: <0.5% [5mm on 1m long sample]
• Yield strength (Rp0.2%)
• Hard/semi hard >120 MPa
• Soft <80 MPa
• Super soft <65 MPa
PV ribbon straightness, also known as camber, is
measured in terms of millimetres off a straight line on one
metre long ribbon sample.
Maximum level of camber is determined by the stringing
process and typically ranges between <8mm/metre and
<5mm/metre.
There are different types of solder compositions used
in PV ribbon. They depend on the stringing/soldering
technique deployed by the panel manufacturer and
the local health and safety standards related to panel
manufacturing.
Common solder compositions are as follows:
• Lead-free solder: Sn 100
• Lead containing solder: SnPb 60/40
• Silver containing solder: SnAg 96.5/3.5; SnAgCu
96.5/3.0/0.5
• Lead and silver containing solder: SnPbAg 62/36/2
• Low temperature solder: BiSn 57/43; BiSnAg 57.7/42/0.3
Solder coat thickness ranges from 10 micron to 40
micron, with tolerances between ±10% and ±30%. The
most common solder coat thickness is 20 micron ±4
micron. There are three types of solder coat thickness
measurement technique:
• X-Ray: off-line measurement used for one-side
thickness measurement
• Manual micrometer: off-line measurement used for
measuring the total thickness of two sides of the coat
• Laser: in-line measurement that can be deployed on
the tinning line and is used for measuring the total
thickness of two sides of the coat during PV ribbon
production
PV ribbon is also inspected visually or with a micro-
scope to examine coating quality, which should be
without defects such as stains, debris, burrs, dents,
discolouration, bare copper visible through solder coating,
small pinholes and other kinds of mechanical defects.
Most of the above specifications and corresponding
measurement techniques are defined in the standards for
PV ribbon that were introduced in August 2011.
❍
❍
Figure 2
: Solar panel with interconnect ribbons soldered onto
cells and bus bar around the panel perimeter
❍
❍
Figure 3
:
Cross-section of a typical hot-dip tinned copper
ribbon