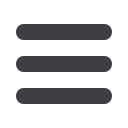

March 2017
•
MechChem Africa
¦
29
⎪
Sustainable energy and energy management
⎪
The complete 35 t packaged diesel generator set being lifted for loading onto transport vehicle.
Preparations underway to start with the scope of work on site, showing the arrival of supporting ancillary
components to be installed, followed by cold and hot commissioning in the presence of specialists from
the DRC Utility, SNEL.
All supporting ancillary components fitted to the mobile substation. Final preparations underway, ready
to commence with connection to the SNEL electrical network.
generator plant
is highly conductive and must not be allowed
to enter the power generationunits,” Gerrard
says. “For this reason, a filter system was
designed that could accommodate the high
volumes of moving air required to cool the
engines, while also requiring as little mainte-
nance as possible.”
Once again, a local solution was designed,
in the form of a custom-engineered, self-
cleaning cartridge type ventilation and pres-
surisation fan unit, comprising four WEG
7.5 kW fan motors.
To feed diesel to the generators, Zest
Energywill install a30000
ℓ
intermediate fuel
tank to draw from the customer’s bulk fuel
storage system with a duplex fuel filtration
and circulation system as well as all inter-
connecting piping, valves, pumps and fittings
within the power plant area.
A local fuel connection point within the
plant area will also be installed as a contin-
gency, shouldbulk fuel supplynot beavailable.
To comply with environmental regulations, a
bunded fuel and oil area will be constructed,
with an oil-water separation system.
“There are also various systems we will
provide for plant auxiliary power require-
ments and for plant earthing and lightning
protection, as well as cabling, terminations,
racking and supports to all plant electrical
equipment,” Gerrard says. “Through our
member companies in the Zest WEG Group,
we are able to give our customers a single
point of contact for the range of services
we are providing, while project managing
and quality controlling every aspect of the
power plant.”
q
tection system, earthing, site work (with full
commissioning and testing) and site training.
The project began in February 2016, and
the unitwas commissioned andhandedover
to the mine developer in October 2016, in
line with a challenging delivery deadline of
nine months.
“Our strong network within the WEG
Group, of which ZestWEGGroup is part, al-
lowedustoworkwithWEGTransmissionand
Distribution inBrazil on transformer design,
manufacturing and factory testing,” Gerrard
says. “We also involved WEG Transformers
Africa – also a Zest WEG Group company –
when it came to site assembly and testing of
the mobile transformer.”
The commissioningprocess includedfinal
assemblyof the transformer, oil filtrationand
purification, and conducting a full spectrum
oftransformertests,aswellason-sitetesting
of all supporting substation equipment. To
ensure strict compliance, all commissioning
and testing was done in conjunction with
SNEL to meet contractual and performance
requirements.
Skills transfer was facilitated by opera-
tor training conducted by Zest Energy to all
selected mine personnel, ensuring that the
substation was left in safe hands, with a
strong after-sales service to respond to any
further customer requirements.
q