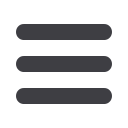

M
ay
2010
93
›
W
elding
T
echnology
Fully automatic welding
process without filling wire
Welding takes place from
inside leaving root outside
For tubular parts either with
saddle or straight weld
Weld
demanding
quality
tubular
parts
technologies for
processing tubular parts
Tel: +358 20 7121 444
Fax: +358 20 7121 449
maarit.aalto@lacol.com www.larikka.comThank you
for
visiting us!
LARIKKA
Collaring
|
Welding
|
Cutting
than
ksilm.indd 216.3.2010 15.46
THE induction high frequency welding
method is a key process technology for the
production of ferrous and non-ferrous tubes
with a diameter range from a few millimetres
up to 26" at wall thicknesses up to 25mm,
for a variety of applications.
Due to the growing product spectrum
of tube and pipe mills, flexible welding
systems are increasingly essential. SMS
Elotherm’s welders accommodate a broad
range of new materials and their alloying
elements, particularly high strength steels
and stainless steels, in a wide variety
of dimensions. Through the optimum
configuration of system parameters and
welding frequencies, a single induction
welder reliably produces high quality weld
seams.
The quality of the welding seam produced
is dependent on a variety of parameters,
including material quality, material
presentation, welding angle, impeder (ferrite
quality), and frequency.
Considering the influenceof the frequency
on the seam quality, higher frequencies are
generally to be preferred for small steel
tubes and thin walls. For wall thickness
greater than 4mm, lower frequencies below
150kHz are favoured.
The
required
impeder-system
concentrates the current flow in the strip
edges and increases the efficiency of the
welding process.
The impeder has to match in diameter
and length with the given tube size, and
should have the maximum possible values
for saturation flux density and amplitude
permeability.
SMS Elotherm has more than 70 years
of experience as a supplier of complete
induction systems for an array
of applications in the tube and
pipe industries. To help tube
and pipe makers improve their
energy efficiency, SMS Elotherm
develops and builds state-of-the-
art converters (power supplies) for
induction systems.
SMS Elotherm GmbH
–
Germany
Fax: +49 2191 891 726
Email:
info@sms-elotherm.deWebsite:
www.sms-elotherm.deHigh frequency induction welding
Tube welding with induction technology
EFD Induction has delivered two of its
Weldac 600kW high frequency induction
IGBT (insulated gate bipolar transistor) tube
welders to tube mills in the Chicago area.
Both systems replaced older vacuum tube
technology in existing tube mills.
The tube producers will use the EFD
Induction Weldacs to weld tube to customer
and industry standards. Both Weldacs
delivered can use contact welding or
induction coil welding methods.
Commenting on the delivery, Mark
Andrus of EFD Induction in the USA said,
“The customers have chosen EFD Weldacs
based on the welders’ high efficiency,
uptime performance, and excellent EFD
Induction customer support. In addition,
these customers now have reported gains
in weld quality.”
The EFD Induction Weldac 600 high
frequency tube welders have a single
footprint layout, automatic load matching,
and customised control packages to offer
a wide range of operational flexibility. The
Weldacs use of IGBT for high frequency
switching allows for maximum ruggedness
in the area of power electronics for solid-
state high frequency tube welding.
EFD states that, along with the good
power factor rating, high electrical efficiency
and high current handling capabilities of the
Weldac, tube production and quality can be
increased.
EFD Induction Inc
– USA
Fax: +1 248 658 0701
Email:
sales@us.efdgroup.netWebsite:
www.efd-induction.comChicago area tube mills opt for
EFD Induction Weldac