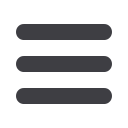

Article technique
Mars 2013
110
www.read-eurowire.comLes variations du flux du gaz non
détectées entraîneront des variations
de capacitance et, par conséquent, une
instabilité du processus avec de grandes
quantités de rebuts.
Les mesurages du flux de l’injecteur hors
ligne (tels que le déplacement de l’eau)
permettent de déterminer le débit moyen
de l’injecteur à la température ambiante.
Toutefois, il ne sera pas possible de
déterminer le débit effectif du processus
ni la variation du débit étant donné
que le débit de l’injecteur peut varier
radicalement après le réchauffage jusqu’à
atteindre les températures de processus.
Il est donc recommandé d’employer un
mesureur de flux en ligne lorsque l’on
obtient l’expansion au moyen d’injection
de gaz.
Avec un mesureur de flux, la pression du
gaz peut être affichée avec précision pour
obtenir le débit calculé requis pour la
capacitance nominale désirée. En outre,
il est possible de contrôler les variations
de débit.
Sélection de l’injecteur
de gaz pour le produit
Lorsqu’un injecteur est dimensionné, il
faut considérer la pression du cylindre
d’extrusion et le débit de l’azote pour
obtenir le taux d’expansion désiré par
rapport à la vitesse d’avancement du
produit. Le flux de gaz dépend des
dimensions de l’orifice de l’injecteur et de
la pression de l’azote.
L’orifice doit être dimensionné de manière
à ce que la pression du gaz soit supérieure
à la pression du cylindre pour obtenir le
flux de gaz désiré.
Supposons qu’une structure de câble
donnée exige un flux de 50cc/minute
d’azote pour une vitesse de ligne de
600 pieds par minute et qu’une pression
du cylindre d’extrusion de 1 000psig soit
générée.
L’injecteur sélectionné pour ce processus
exige que l’orifice ait des dimensions
adéquates pour obtenir un débit de gaz de
50cc/minute à une pression supérieure à la
pression du cylindre.
Avec un flux supérieur à 50cc/minute à
1 000psig, la pression du gaz devrait être
réglée à une valeur inférieure à la pression
du cylindre; toutefois cela produirait une
obstruction qui à son tour causerait la
solidification du produit.
En augmentant la pression du gaz à des
valeurs supérieures à 1 000psig, le flux
de gaz serait trop élevé et causerait une
expansion excessive. Cette formation
de mousse excessive est souvent mal
comprise et considérée comme étant un
problème dû au matériau ou au processus.
Au contraire, si l’orifice de l’injecteur est
trop petit, la pression du gaz disponible
pourrait ne pas être suffisante pour
obtenir le flux de gaz requis.
Cela empêchera d’obtenir le taux
d’expansion et la capacitance du produit
désirés. Généralement, pour cette raison
on utilise plusieurs injecteurs avec
différents flux disponibles pour une
▲
▲
Figure 6
:
Section transversale d’un noyau de
large gamme de pressions. Le nombre de
dimensions différentes nécessaires varie
selon la gamme de produits et la pression
du gaz disponible. L’utilisation d’une
pompe d’azote à haute pression augmente
la gamme de pressions de gaz disponibles
par rapport à l’utilisation d’un cylindre à
haute pression.
L’utilisation d’une pompe peut donc
contribuer à réduire le nombre de
dimensions des injecteurs requis pour une
opération ainsi que les coûts totaux.
Les performances peuvent être influen-
cées également par la conception de
l’injecteur.
La
Figure 5
illustre les résultats des essais
basés sur la comparaison de quatre types
d’injecteurs disponibles sur le marché
obtenus en mesurant la variation de flux
du gaz et la variation de la capacitance
en résultant. Pou ces essais on a utilisé un
noyau de 50Ohm avec un conducteur de
diamètre 23G expansé jusqu’à environ
50 pour cent.
La variation Six Sigma du flux de gaz
(± 3 déviations standard) allait de 4cc/
min à 27cc/min avec une variation de
capacitance résultante allant de 0,3 à
3,8pf/ft. Ces résultats démontrent que
les problèmes de performance, souvent
attribués
au
fluoropolymère,
sont
typiquement des problèmes de processus
liés aux équipements.
L’utilisation
d’un
injecteur
mal
dimensionné
ou
d’une
structure
instable peut cacher le bénéfice réel des
performances de certains matériaux.
Refroidissement
du produit
Généralement,
le
moyen
de
refroidissement pour le noyau extrudé
consiste en une combinaison d’air
ambiante et eau.
La distance requise pour chacune de
ces dernières dépend des dimensions
du produit et de la vitesse de la
ligne. Les distances correctes sont
fondamentales pour le refroidissement
avant l’enroulement du fil pour éviter
l’aplatissage de l’isolement sur le dévidoir
et un impact sur les performances
électriques.
En maintenant la distance du point de
refroidissement de l’eau le plus loin
possible de la tête d’injection, on peut
obtenir un produit meilleur. Et ce, parce
qu’une distance suffisante du point de
refroidissement au moyen d’air permet
la contraction de la résine au-dessus du